The Critical Role of Vacuum Filling Machine Manufacturers in Modern Production
In today’s competitive manufacturing landscape, maximizing output and efficiency is not just a goal; it’s a necessity. Vacuum filling machines represent a sophisticated technology crucial for industries demanding precise, contamination-free packaging, particularly in sectors like food, beverages, pharmaceuticals, and cosmetics. While various equipment options exist, collaborating directly with a specialized vacuum filling machine manufacturer offers distinct advantages for businesses aiming to boost their output rapidly and sustainably.
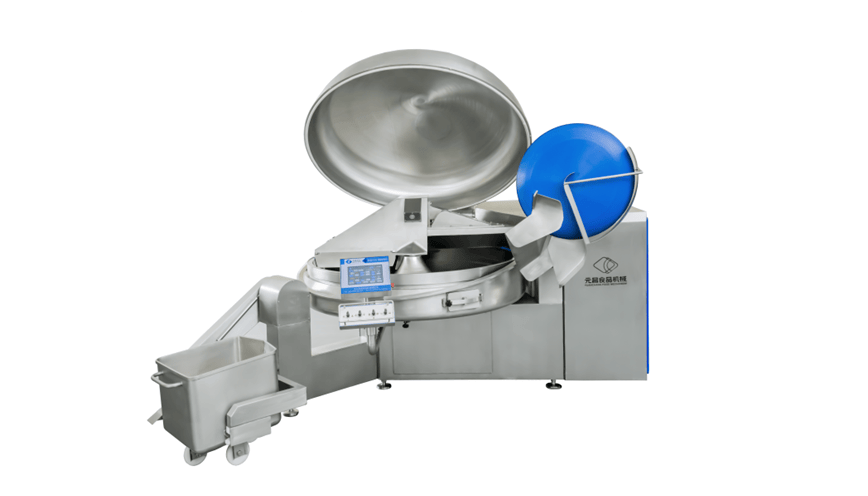
Choosing a dedicated manufacturer provides access to deep technical expertise and innovative design principles developed specifically for vacuum technology. These manufacturers possess intricate knowledge of creating machines that generate consistent, high-quality vacuum levels essential for preserving product integrity, extending shelf life, and ensuring precise fill volumes without leaks or spillage. Their understanding extends beyond the machine itself, encompassing the unique challenges of different product viscosities, container types, and stringent hygiene protocols.
Unlocking Production Velocity: Four Manufacturer-Enabled Strategies
The path to significantly enhanced output is multifaceted. Partnering with a knowledgeable vacuum filling machine manufacturer empowers businesses to implement key strategies effectively:
Method 1: Leveraging Custom-Engineered Automation and Scalability
Off-the-shelf solutions often fail to match the unique pace or complexity of a specific production line. Leading manufacturers excel in designing bespoke vacuum filling systems. This involves engineering machines tailored to exact throughput requirements, container specifications, and integration needs with upstream and downstream equipment. Such customization eliminates bottlenecks caused by mismatched machinery. Furthermore, forward-thinking manufacturers build in scalability from the outset. Machines designed with modular architecture allow for seamless throughput upgrades – adding filling heads, automating cap feeding, or integrating faster conveyors can be executed efficiently as demand grows. This proactive approach ensures the filling operation keeps pace without complete line overhauls.
Method 2: Implementing Advanced Sealing and Vacuum Control Technology
Filling speed is intrinsically linked to the efficiency and reliability of the vacuum sealing process. Specialized manufacturers continuously innovate in this core area. Utilizing machines equipped with precision vacuum pumps and sophisticated control systems ensures rapid evacuation of air from containers and consistent vacuum levels cycle after cycle. Advanced sealing mechanisms are crucial for maintaining hermetic seal integrity reliably at higher speeds. Manufacturers understand the nuances – using durable sealing materials compatible with the product, optimizing seal bar timing and pressure, and incorporating fail-safes. This technological edge minimizes leaks, seal failures, and product waste, directly translating to higher usable output and reduced downtime for adjustments.
Method 3: Integrating Optimized Cleaning and Changeover Systems
Downtime during cleaning and product changeovers is a significant thief of potential output. Specialized manufacturers address this by engineering machines with Cleaning-in-Place (CIP) and sometimes Sterilization-in-Place (SIP) capabilities directly into the design. Optimized CIP systems, designed specifically for the machine’s internal pathways and filling nozzles, enable thorough cleaning without major disassembly, drastically reducing the time machines are offline. Similarly, quick-change tooling systems for nozzles, pistons (if applicable), and container handling parts, often developed as manufacturer-specific solutions, facilitate rapid switching between different products or container sizes. This minimizes transition times and maximizes productive machine hours.
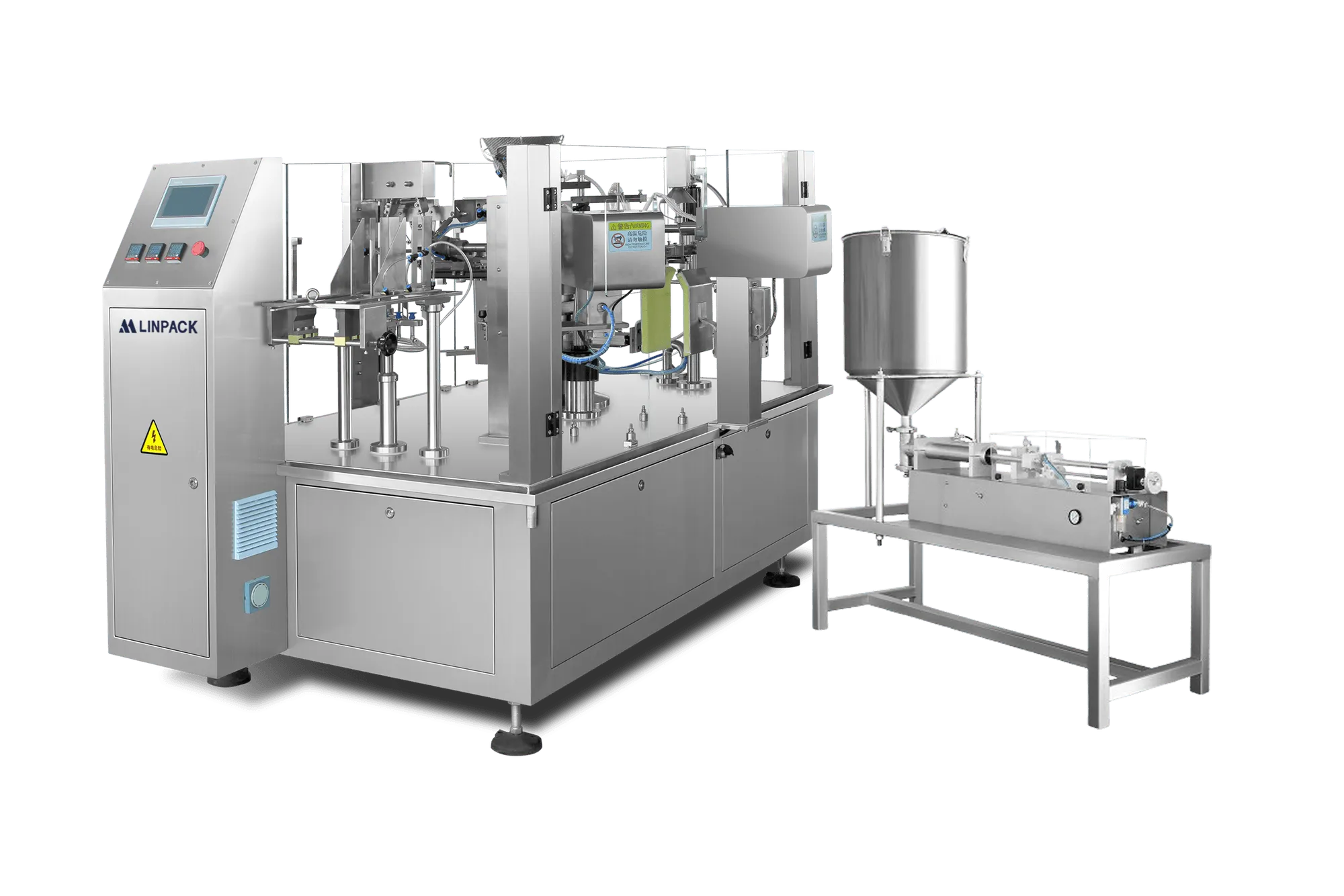
Method 4: Leveraging Manufacturer-Driven Predictive Maintenance and Support
Unplanned machine breakdowns severely hamper output goals. Leading vacuum filling machine manufacturers provide more than just the initial equipment. They offer comprehensive support programs built on their in-depth knowledge. This includes sophisticated remote monitoring capabilities that track machine performance parameters. Combined with the manufacturer’s experience, this data enables predictive maintenance scheduling – identifying potential wear points like specific seals or pump components before they fail catastrophically. Access to readily available genuine spare parts and priority technical support from engineers intimately familiar with the machine’s design ensures rapid resolution of any issues. This proactive maintenance approach, guided by the manufacturer’s expertise, significantly enhances overall equipment effectiveness (OEE) by reducing unexpected downtime.
Manufacturer Partnership: The Foundation for Accelerated Growth
Boosting production output quickly requires a strategic approach to the core filling technology. A vacuum filling machine manufacturer brings the specialized knowledge, technological innovation, and tailored solutions necessary to overcome common production constraints. Their expertise in custom automation, advanced vacuum/sealing control, rapid changeover design, and proactive maintenance support provides a robust foundation. By choosing a manufacturer that prioritizes these elements, businesses can unlock significant gains in speed, reliability, and efficiency, achieving their accelerated output objectives while maintaining the highest standards of product quality and safety.