Vacuum rollers are specialized components widely utilized in industrial settings where secure transport and precise handling of flat, flexible materials are essential. Functioning on the principle of suction or negative pressure, these rollers offer a non-mechanical grip, making them highly versatile across numerous applications.
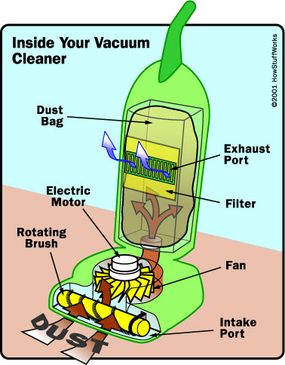
Understanding the Core Function
At its essence, a vacuum roller comprises a perforated cylindrical surface connected internally to a source of vacuum. When vacuum is applied within the roller, atmospheric pressure pushes the material firmly against the roller’s outer surface through these perforations. This creates a controlled holding force. The key components typically include:
- Perforated Roller Surface: Features precisely drilled holes or slots through which the vacuum is applied. The pattern and density influence the holding strength and suitability for different materials.
- Stationary Internal Vacuum Chamber: Mounted inside the rotating roller cylinder. This chamber maintains a constant vacuum zone across a defined arc of the roller’s rotation.
- Bearings & Seals: Enable the roller cylinder to rotate freely around the fixed vacuum chamber while maintaining the vacuum seal.
- Vacuum Source Connection: An external port connects the internal vacuum chamber to a pump or central vacuum system.
- Optional Features: These may include variable vacuum control valves, sensors, or specialized surface coatings for grip or material protection.
Primary Uses Across Industries
Vacuum rollers are indispensable in processes requiring smooth, controlled movement and registration of sheet materials without mechanical clamping or pins. Their non-marking grip is a significant advantage. Common applications span:
- Packaging & Converting: Unwinding rolls of film, foil, or paper without slippage; transporting delicate sheets through printing presses, laminators, and die-cutters; feeding cartons and labels; handling non-slip surfaces like waxed paper.
- Printing Industry: Feeding sheets into presses with precision registration; gripping printed sheets for transport without smudging; handling coated or varnished papers.
- Textile & Nonwovens: Guiding fabric webs through spreading, coating, or cutting machines; handling knit materials prone to stretching; managing materials without mechanical stress.
- Paper & Board Processing: Feeding heavy paperboard or corrugated sheets smoothly; handling large paper sheets in finishing operations; maintaining alignment.
- Plastics & Films: Transporting thin, fragile films in production lines; handling multiple layers; moving slippery plastic sheets during thermoforming or cutting.
- Automation & Robotics: Integrated into robotic end-effectors for pick-and-place tasks involving sheets, particularly when gentle handling or repositioning without surface contact is needed.
- Electronics Manufacturing: Transporting delicate circuit boards or panels through assembly lines; handling thin wafers or films during fabrication.
Key Functional Benefits
The widespread adoption of vacuum rollers stems from their distinct functional advantages:
- Non-Mechanical, Non-Marking Grip: The suction principle eliminates the need for clamps, pins, or aggressive gripper surfaces, virtually eliminating surface damage, impressions, or tears on delicate materials.
- Highly Secure Transport: Vacuum holds the material firmly to the roller surface, preventing slippage and ensuring consistent feed speed. This is critical for registration accuracy in printing and converting.
- Accelerated Handling Speeds: By providing a reliable grip, vacuum rollers enable higher operational line speeds compared to methods prone to slippage or requiring frequent operator intervention.
- Handling Diverse Materials: They excel with materials that are difficult to grip mechanically – thin films, delicate textiles, slippery coatings, rigid boards, and even perforated or textured sheets where suction can still be effective across solid areas.
- Minimal Maintenance: Compared to some complex mechanical grippers or high-friction surfaces, vacuum rollers often have fewer moving parts in direct contact and require less intensive maintenance.
- Constant Tension Control: Especially when used as unwind/rewind assist rollers, they provide a smooth, low-inertia braking or feeding force, improving tension control.
- Material Integrity Preservation: Gentle gripping preserves the physical properties and surface qualities of sensitive materials.
Critical Selection Considerations
Choosing the right vacuum roller requires careful evaluation of several parameters:
- Material Properties: Thickness, permeability, surface smoothness, and rigidity heavily influence the required hole pattern, vacuum level, and roller diameter.
- Required Holding Force: Determined by material weight, line speed, acceleration/deceleration forces, and the friction needed to prevent slippage. Larger rollers or higher vacuum levels increase force.
- Vacuum Arc Size: The angular length of the vacuum zone affects how much material is held in contact at any given time. This impacts wrapping and release characteristics.
- Compatibility with Equipment: Dimensions, mounting style, shaft connections, and rotational speeds must integrate seamlessly with existing machinery.
- Hole Pattern & Roller Surface: Should be optimized for the specific material to avoid marking while ensuring adequate flow. Specialized coatings can aid release or enhance grip on particular surfaces.
By providing a secure, non-marking method of transporting flat materials, vacuum rollers significantly enhance efficiency, quality, and reliability in countless manufacturing processes. Their design harnesses the simple power of vacuum to solve complex handling challenges across diverse industries.