Maintaining the quality of sweet potatoes from farm to market demands meticulous cleaning. Traditional methods, often labor-intensive and inconsistent, struggle to efficiently remove dirt and debris without damaging the delicate tubers. Specialized equipment designed specifically for sweet potatoes offers a more reliable and efficient solution.
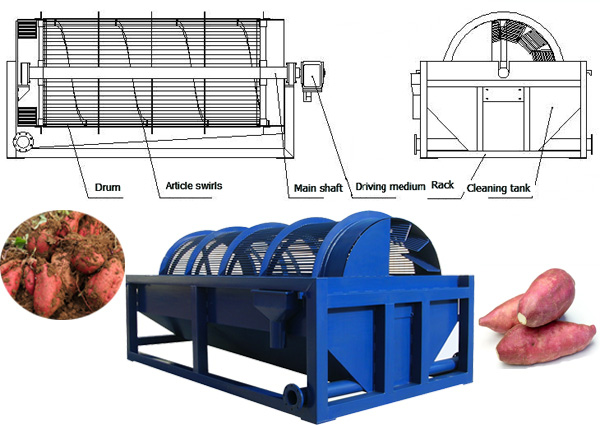
The Challenges of Sweet Potato Cleaning
Sweet potatoes present unique cleaning hurdles. Their often irregular shapes, with bumps and indentations, trap soil effectively. The skin, while durable, is susceptible to bruising and scratching during washing, potentially reducing shelf life and market value. High-output agricultural operations require methods that are not only gentle but significantly faster than manual scrubbing or basic water rinsing.
Unlocking Efficiency with Purpose-Built Machinery
Modern sweet potato washing machines address these challenges through targeted engineering:
- High-Pressure, Gentle Spray Systems: Strategically placed nozzles deliver powerful water jets precisely angled to dislodge dirt clods and fine particles from grooves and crevices. The pressure is carefully calibrated to be effective without compromising skin integrity.
- Rotating Brush Mechanisms: Complimenting the water jets, soft-bristled or sponge-like rollers gently agitate the tubers. These brushes assist in loosening stubborn mud and provide a mild polishing effect, enhancing the natural appearance of the produce.
- Conveyorized Handling: Tubers travel smoothly through the cleaning stages on specialized belts or rollers. This continuous flow minimizes impact and handling damage while ensuring uniform exposure to water jets and brushes.
- Multi-Stage Rinsing: Efficient machines often incorporate separate chambers for initial heavy soil removal and subsequent thorough rinsing. This staged approach ensures cleaner results and can be designed for water efficiency.
Key Elements for Effective Cleaning
Optimizing the cleaning process involves attention to several factors:
- Water Management: Utilizing filtration systems to recirculate water reduces consumption. Water pressure and volume need constant monitoring to balance effectiveness with conservation and to prevent oversaturation of the tubers.
- Optimal Brush Contact: Brush type, density, and rotation speed require adjustment based on sweet potato variety, soil type, and desired finish. The goal is effective cleaning without abrasion.
- Timing & Throughput: Ensuring tubers spend sufficient time in each cleaning stage is vital. Machine speed must be calibrated to the unit’s design capacity to guarantee thorough cleaning without bottlenecks.
- Pre-Sorting: Removing large stones, vines, and severely damaged tubers before washing prevents equipment jams and protects the machine mechanisms.
Measuring the Efficiency Gains
The implementation of specialized cleaning technology brings tangible benefits:
- Enhanced Cleaning Efficacy: Purpose-built machines achieve a significantly higher degree of cleanliness compared to rudimentary methods, leaving tubers ready for packing or minimal post-wash touch-ups.
- Significant Labor Reduction: Automated washing drastically cuts the manual labor required for this task, freeing up workers for other crucial operations.
- Improved Product Quality and Shelf Life: Gentle, controlled cleaning minimizes skin damage, reducing entry points for rot and decay. This translates to less spoilage in storage and transit, ensuring fresher produce reaches consumers.
- Increased Processing Speed: Designed for volume, these machines process tubers much faster than manual methods, crucial for handling large harvests efficiently.
- Water Conservation: Closed-loop systems with filtration allow for significant water reuse, lowering the environmental footprint and operational costs associated with fresh water consumption.
Integrating Cleaning into the Workflow
For maximum efficiency, the washing machine should seamlessly integrate into the post-harvest line. Positioning it after initial destoning or vine removal and before grading or sizing stations ensures smooth workflow progression. Regular maintenance of spray nozzles, brushes, and filtration systems is essential to sustain peak performance and water efficiency over time.
A Vital Step Towards Market Success
In the competitive agricultural market, the appearance and quality of sweet potatoes are paramount. Implementing efficient washing technology is no longer a luxury but a practical necessity for producers aiming for scale, consistency, and profitability. The methods revealed through this specialized equipment—combining targeted high-pressure water, gentle agitation, and efficient handling—deliver on the promise of clean, undamaged, shelf-stable produce essential for meeting the demands of modern consumers.