Industrial mixing processes face consistent pressure to enhance efficiency while controlling expenses. The large vacuum roller kneading machine emerges as a critical asset in this endeavor, offering significant potential for operational cost reduction. These robust machines, combining the mechanical action of rollers with controlled vacuum environments, excel at processing viscous materials like rubber, silicone, and polymers. Utilizing them effectively requires strategic implementation beyond mere operation. Here are four professional tips to maximize cost savings with this equipment:
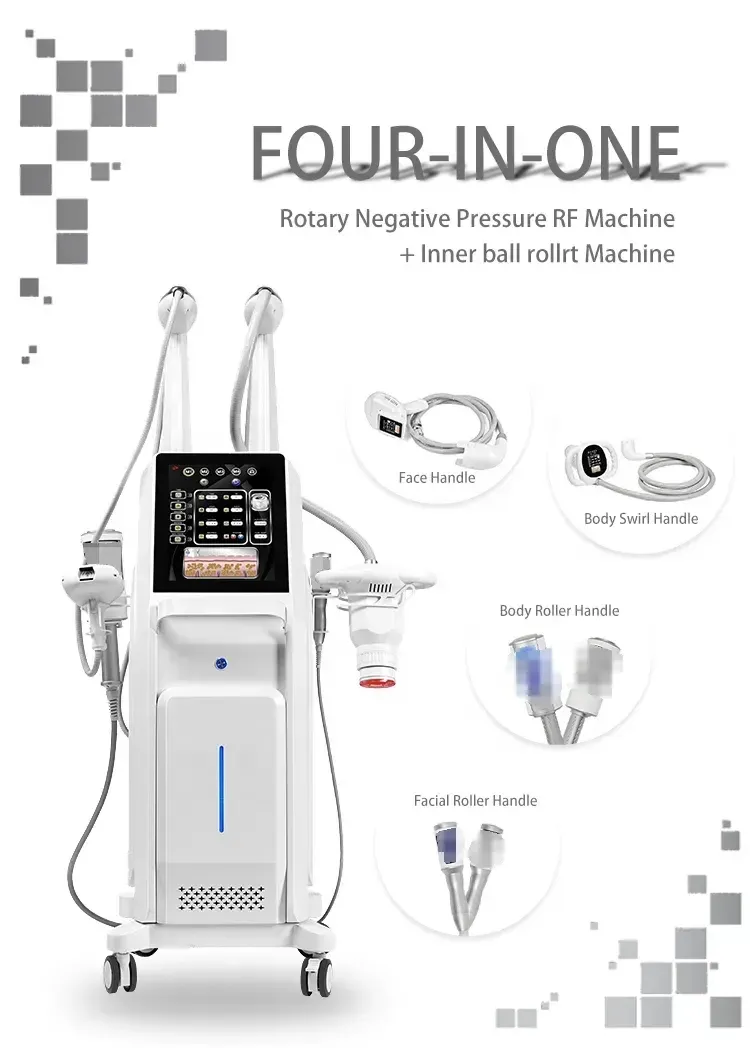
1. Optimize Material Preparation & Batching
Significant savings begin before the material even enters the mixer. Precise weighing and accurate formulation adherence are non-negotiable. Utilizing scales calibrated regularly minimizes costly errors in raw material usage. Furthermore, establishing efficient staging sequences ensures materials are readily accessible near the machine, reducing idle time during loading. Pre-cutting large rubber bales or pre-warming specific additives (as per manufacturer guidelines) can streamline the feeding process, accelerating the overall cycle time. This meticulous approach to preparation reduces material waste and improves batch consistency from the outset.
2. Master Vacuum Cycle Management
The vacuum function is central to the machine’s capability, eliminating air bubbles and preventing porosity, which improves product quality and reduces waste from defects. Understanding the optimal vacuum level and duration for each specific material recipe is crucial. Applying excessive vacuum unnecessarily prolongs cycle times and consumes extra energy, while insufficient vacuum leads to subpar product quality and potential scrap. Operators should fine-tune the vacuum cycle based on the material’s characteristics and batch size, consulting technical data sheets and experimenting cautiously under controlled conditions to find the most efficient settings that guarantee quality without waste.
3. Implement Predictive & Preventative Maintenance
Large vacuum roller kneaders represent a substantial capital investment. Protecting this investment through proactive maintenance is a direct line to long-term savings. Moving beyond reactive fixes to a schedule-based and condition-monitoring approach is essential. Regularly scheduled lubrication of bearings, gearboxes, and moving parts minimizes friction-induced wear and unexpected failures. Monitoring oil levels, checking hydraulic hoses for wear, and inspecting seals (especially around the vacuum chamber) should be routine. Leveraging vibration analysis or temperature monitoring on critical components like drive motors and rollers can help identify potential issues early, preventing costly catastrophic breakdowns and extending the machine’s operational life significantly.
4. Enhance Operator Training & Process Standardization
Operator expertise directly impacts machine efficiency and resource utilization. Comprehensive, ongoing training is vital. Operators should be thoroughly trained not only in safe machine operation but also in understanding the nuances of different material behaviors, the impact of process parameters (temperature, mixing time, vacuum settings), and basic troubleshooting techniques. Standardized Operating Procedures (SOPs) ensure consistent practices across all shifts, guaranteeing uniform product quality and preventing variations that lead to waste. Empowering operators with knowledge about how their actions affect costs – material usage, energy consumption, and downtime – fosters a cost-conscious operational culture.
Adopting these professional strategies allows manufacturers to unlock the full cost-saving potential inherent in large vacuum roller kneading machines. From optimizing inputs and refining critical processes to safeguarding machinery and empowering personnel, these approaches focus on operational excellence. The result is a tangible reduction in material waste, lower energy consumption per unit produced, minimized unplanned downtime, and maximized throughput, driving significant improvements to the bottom line while maintaining high standards of product quality.