The Efficiency Revolution in Potato Farming
Modern agriculture constantly seeks innovations that streamline operations, and potato cleaning machines represent a significant advancement. Unlike traditional manual cleaning methods, these automated systems address two critical pain points for farmers: excessive time consumption and unsustainable water usage.
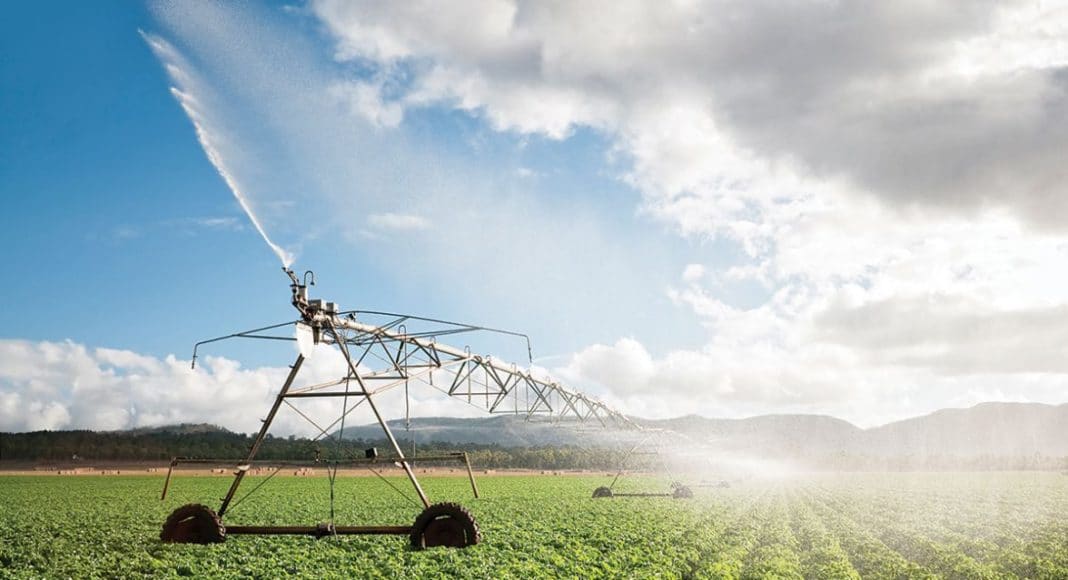
Transforming Labor-Intensive Processes
Manual potato cleaning requires teams of workers scrubbing each tuber individually, a process taking up to 50 minutes per 100kg batch. Cleaning machines accomplish the same task in under 15 minutes. This efficiency stems from integrated systems where rotating brushes, adjustable pressure nozzles, and conveyor belts work simultaneously. One farmer in Idaho reported processing 2.5 tons hourly using a single machine – a volume that previously demanded eight laborers working full shifts.
The automation extends beyond cleaning to sorting and grading. Optical sensors detect defects while brushes remove clumped soil without damaging the skin. This consolidated workflow eliminates repetitive tasks and reduces staffing needs during harvest peaks.
Water Conservation Mechanisms
Traditional cleaning consumes 300-400 liters per ton of potatoes through continuous rinsing. Modern machines incorporate three key water-saving features:
- Closed-loop filtration: Up to 80% of water gets recycled through sedimentation tanks and UV sterilization
- Targeted spray nozzles: Directional jets focus only where needed, cutting usage by 40%
- Moisture sensors: Automatically regulate flow based on soil residue levels
Field tests in the Netherlands demonstrated 65% less water consumption versus bucket-rinsing methods. For farms relying on well water or facing drought restrictions, these savings translate directly to cost reductions and environmental compliance.
Operational Advantages Beyond Efficiency
Though time and water savings are paramount, secondary benefits enhance profitability:
- Reduced crop damage: Gentle roller systems maintain potato integrity better than manual handling
- Improved marketability: Consistent cleaning quality meets supermarket cosmetic standards
- Labor reallocation: Workers shift from cleaning to higher-value tasks like quality control
The scalability accommodates diverse operations – compact models serve smallholdings processing 500kg daily, while industrial versions handle 20-ton loads. Most machines operate on standard farm electricity and require minimal maintenance beyond routine brush replacement.
Economic Implications
Initial investment costs get offset within two growing seasons through resource savings. A French cooperative calculated recovery of machine expenses in 18 months based on:
- 60% reduction in hourly labor costs
- Lower water bills and disposal fees
- Higher premiums for unblemished produce
The continuous operation capability proves invaluable during harvest windows when delays cause spoilage. Growers gain flexibility to respond to market demands without being bottlenecked by cleaning capacity.
Sustainable Progress
Potato cleaning machines exemplify agricultural innovation where productivity and resource conservation align. By simultaneously addressing temporal and environmental pressures, these systems help farmers build resilient operations. As water scarcity concerns grow and labor availability fluctuates, such technology transitions from luxury to operational necessity for competitive farming enterprises.