Understanding potato washer machine pricing requires examining several technical and commercial factors. Commercial-grade equipment differs significantly from consumer models, particularly in durability, throughput, and overall system complexity. Price variations reflect these fundamental differences in engineering and application.
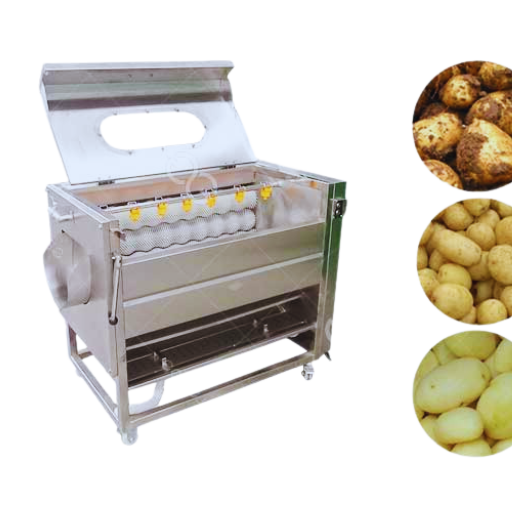
Key Factors Influencing Potato Washer Machine Prices
Several core elements dictate the investment required for a potato washer:
- Capacity and Throughput: Larger machines designed for high-volume industrial processing (e.g., thousands of pounds per hour) command significantly higher prices than smaller units suited for farms or modest food service operations.
- Construction and Durability: Machines built with robust materials like high-grade stainless steel (e.g., SUS304/SUS316) resist corrosion and endure harsh cleaning environments longer than those using lighter gauge or lower-grade materials, impacting longevity and upfront cost.
- Automation and Features: Basic models involve manual loading/unloading. Prices increase substantially with added automation like conveyors, integrated brush systems, variable speed drives, water filtration/recycling systems, and touch-screen PLC controls for optimizing wash cycles.
- Water and Energy Efficiency: Designs incorporating efficient water pumps, spray nozzles, and potential recirculation systems may have a higher initial cost but offer significant long-term savings on utility bills and water treatment.
- Brand Reputation and After-Sales Support: Established manufacturers with proven reliability, warranties, technical support networks, and readily available spare parts often price their machines higher than lesser-known competitors.
- Market Location and Shipping: Geographic factors influence final cost. Machines manufactured locally may avoid hefty import duties and complex logistics fees associated with international shipping.
Beyond these core factors, custom modifications, such as specific brush types for different potato varieties or specialized rinsing configurations, will further elevate the price point.
Cost-Effective Maintenance: Preserving Value and Performance
A well-maintained potato washer operates efficiently for years, minimizing the effective cost per use. Neglecting maintenance leads to accelerated wear, frequent breakdowns, higher energy/water consumption, and costly downtime or replacements.
Essential Cleaning Protocols
Daily and post-operation cleaning is non-negotiable:
- Post-Shutdown Rinse: Use clean water immediately after stopping the machine to flush away all potato debris, soil, and organic matter clinging to surfaces, brushes, and tanks.
- Thorough Internal Cleaning: Periodically, deep clean all accessible parts – tanks, drum interiors, brushes, spray arms, and conveyors. Remove any accumulated residue to prevent bacterial growth and clogging.
- Drain and Tank Sanitization: Regularly drain, clean, and sanitize all water tanks and reservoirs using appropriate food-grade cleaning agents to eliminate biofilm and pathogens.
- Exterior Wipe-Down: Keep external surfaces clean to prevent grime buildup that can eventually migrate internally.
Routine Component Inspection and Care
Proactive checks prevent minor issues from escalating:
- Brush Wear: Inspect brush bristles routinely. Worn or damaged brushes reduce cleaning efficiency and can damage produce. Replace brushes according to manufacturer guidelines or when significant wear is evident.
- Bearing Lubrication: Ensure all bearings (especially on drum shafts and rollers) are lubricated at the intervals specified by the manufacturer using the correct lubricant to prevent seizing.
- Spray Nozzle Checks: Examine spray nozzles for clogs or damage. Blocked or misaligned nozzles compromise cleaning effectiveness and waste water.
- Belt and Chain Tension: Regularly check tension on drive belts and chains, adjusting according to the machine’s manual to prevent slippage or excessive wear.
- Electrical Connections: Visually inspect power cords and plugs for damage. Ensure control panels are clean, dry, and free from moisture ingress.
- Seal and Gasket Integrity: Inspect seals and gaskets around tanks, doors, and bearings for leaks or deterioration, replacing them promptly to prevent water damage and maintain hygiene.
Operational Best Practices
How the machine is used directly impacts its longevity:
- Avoid Overloading: Respect the rated capacity. Overloading strains motors, bearings, and structural components, leading to premature failure.
- Pre-Sorting Produce: Remove large stones, clumps of heavy mud, or rotten potatoes before washing to minimize damage to brushes and internal mechanisms.
- Quality Water Source: Use water that meets potable standards whenever feasible. Excessive sediment or contaminants can cause internal scaling and component damage.
- Scheduled Professional Servicing: Adhere strictly to the manufacturer’s recommended service schedule for comprehensive inspections and preventative maintenance by qualified technicians.
Investing in a potato washer involves weighing the upfront price against long-term operational costs. Factors like capacity needs, required durability, and desired automation level define the initial budget. However, true economy is achieved through meticulous, consistent maintenance. By implementing rigorous cleaning routines, proactive component checks, and careful operation, businesses ensure their machine operates reliably at peak efficiency, maximizes lifespan, and delivers the best possible return on investment over time. This disciplined approach transforms even a mid-range machine into a highly cost-effective asset.