The Evolution of Core Vacuum Rolling Technology
The manufacturing landscape for vacuum rolling machines is witnessing significant advancements driven by the need for higher precision, greater efficiency, and reduced operational costs. Leading manufacturers are pushing boundaries, developing systems that cater to increasingly demanding production environments across industries like aerospace, automotive, electronics, and specialty materials.
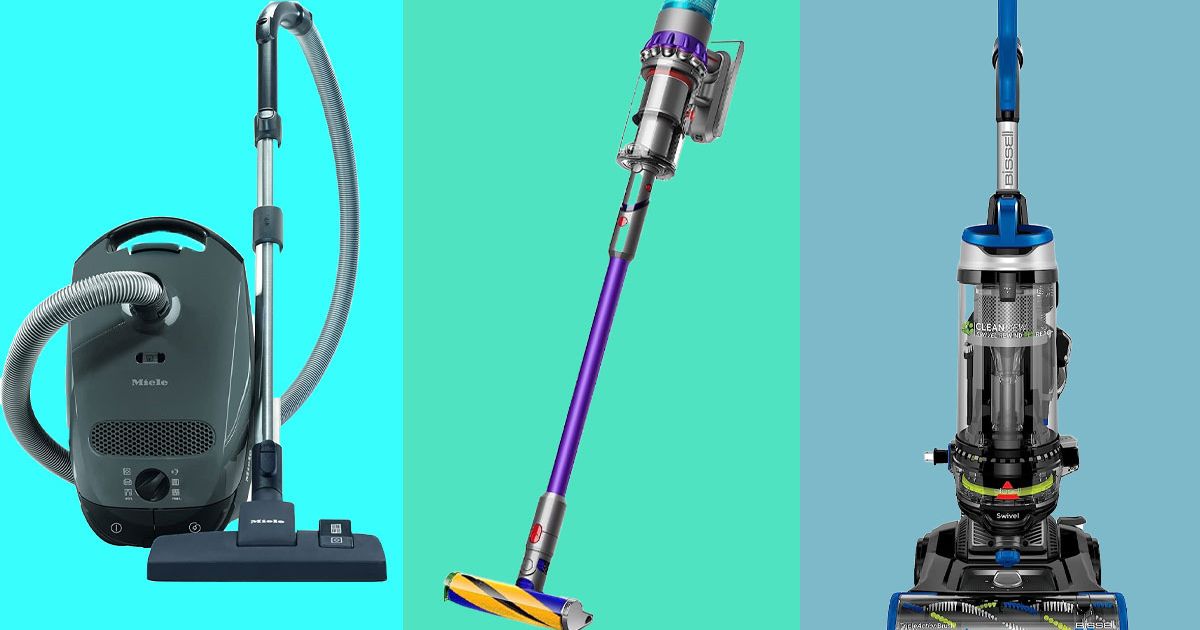
At the heart of recent innovations lie enhancements to the core rolling mechanisms and vacuum systems. New designs incorporate ultra-precise servo motors controlling roll positioning, ensuring micron-level accuracy during material compaction or lamination processes. Concurrently, vacuum systems have seen improvements in sealing technologies and pumping efficiency, drastically reducing cycle times by achieving target pressures faster and maintaining consistent vacuum integrity throughout operations.
Enhanced Control and Data Integration
Modern vacuum rolling machines are increasingly sophisticated command centers. Next-generation Human-Machine Interfaces (HMIs) are transitioning towards large, intuitive touchscreens, offering operators simplified control over complex processes. These interfaces provide real-time visualization of critical parameters such as pressure, temperature, roll speed, and force, enabling immediate adjustments for optimal results.
The integration of Industrial Internet of Things (IIoT) capabilities marks a significant shift. Advanced sensors embedded throughout the machine collect extensive operational data, feeding into cloud-based or on-premise analytics platforms. This connectivity allows for predictive maintenance alerts, remote monitoring by technical support teams, comprehensive process documentation for traceability, and deep performance analysis to identify potential bottlenecks and optimize production workflows for maximum yield.
Focus Areas Driving Innovation
Several key areas are receiving focused attention from top manufacturers:
- Automation Integration: Compatibility with robotic systems for automated loading/unloading is becoming standard. Sophisticated vision systems guide material placement and perform post-process inspection checks, minimizing manual intervention and reducing the risk of defects.
- Energy Efficiency: Significant R&D is directed towards reducing the energy footprint. Innovations include regenerative drive systems, optimized thermal management solutions, and the use of high-efficiency vacuum pumps, leading to lower operational costs and a reduced environmental impact.
- Material Handling Versatility: Machines are being designed to handle a wider spectrum of materials, from delicate films and composites to thicker, more rigid laminates. Adjustable temperature zones across rolls, variable nip pressure profiles, and specialized surface treatments ensure consistent results regardless of material challenges.
Prioritizing Safety and Ergonomics
Innovation extends beyond performance to encompass the well-being of operators. Newer models incorporate advanced safety features like light curtains, emergency stop interlocks at multiple access points, and automated chamber venting procedures before opening. Ergonomic designs reduce operator fatigue through better workstation layouts, reduced noise levels from enclosed machinery and quieter pumps, and simplified access panels for routine maintenance tasks.
Manufacturers are placing greater emphasis on developing comprehensive safety protocols that are seamlessly integrated into the machine’s control logic, minimizing human error and ensuring a secure working environment is paramount in the design philosophy.
Demand-Driven Customization
Recognizing the diverse needs of different industries and applications, the ability to customize vacuum rolling machines is more prevalent than ever. Leading manufacturers now offer a high degree of modularity in their designs. Options range from adjustable roll widths and diameters to specialized chamber configurations, unique material transport systems within the vacuum environment, and integration capabilities for specific auxiliary equipment like plasma treatment units or precision pre-heating stations.
This shift towards tailored solutions allows manufacturers to provide equipment that precisely aligns with a customer’s specific production challenges and quality requirements, moving beyond one-size-fits-all approaches.
The Road Ahead
The pace of innovation in vacuum rolling machinery shows no sign of slowing. Key trends anticipated to shape future developments include the deeper integration of artificial intelligence for autonomous process optimization, further miniaturization for specialized applications like flexible electronics, and continued strides towards completely automated, “lights-out” manufacturing cells.
Understanding these current innovations is essential for any organization reliant on vacuum rolling technology. The advancements made by leading manufacturers are directly addressing industry pain points, offering tangible benefits in productivity, product quality, operational costs, and workplace safety, thereby shaping the future of critical manufacturing processes.
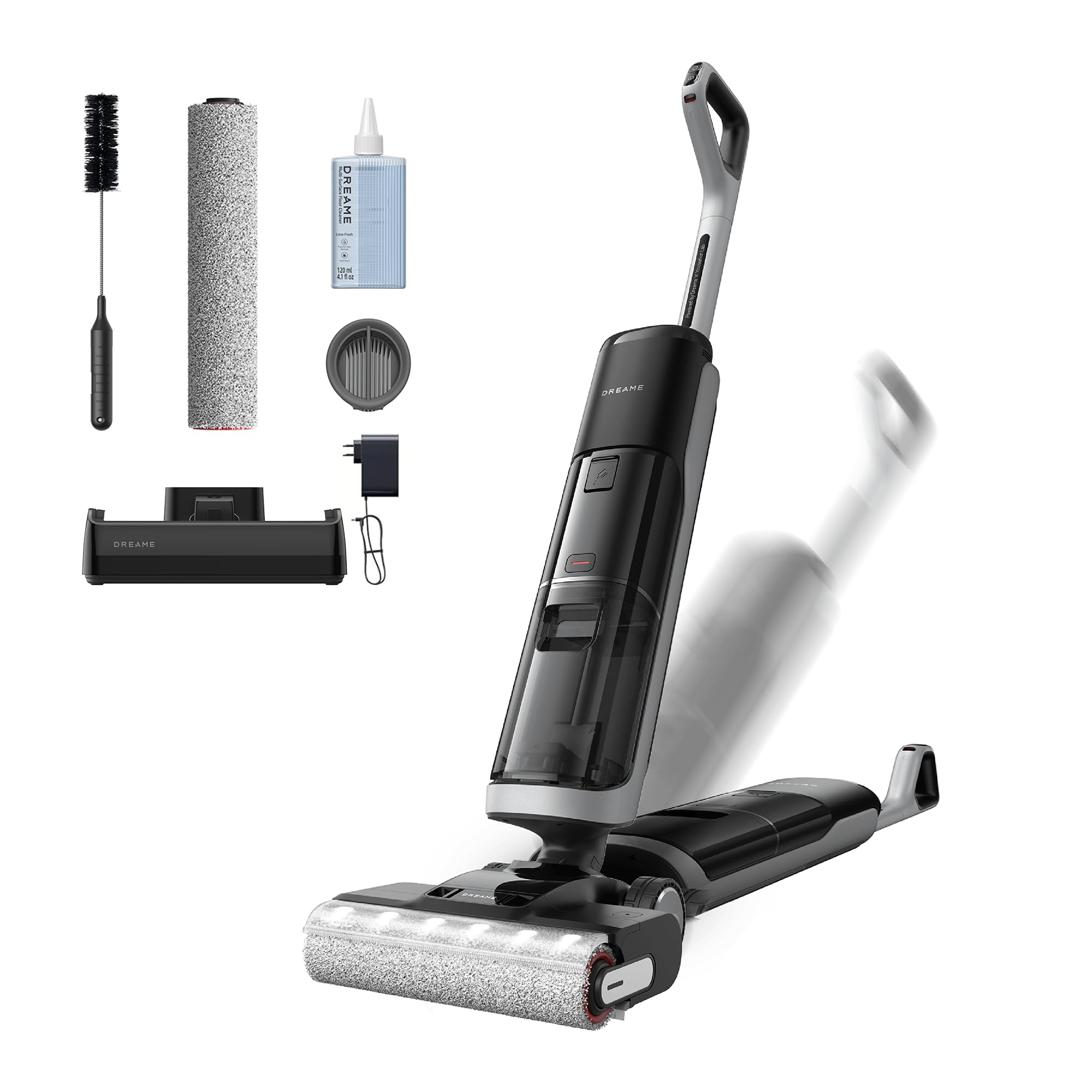