Finding the optimal solution for industrial dewatering needs is crucial for efficient operation across numerous sectors like food processing, chemical manufacturing, mining, pulp and paper production, and wastewater treatment. Industrial Horizontal Dewatering Machines play a pivotal role in this process, separating liquid from solid materials. Understanding the best types available is the first step towards identifying your perfect match.
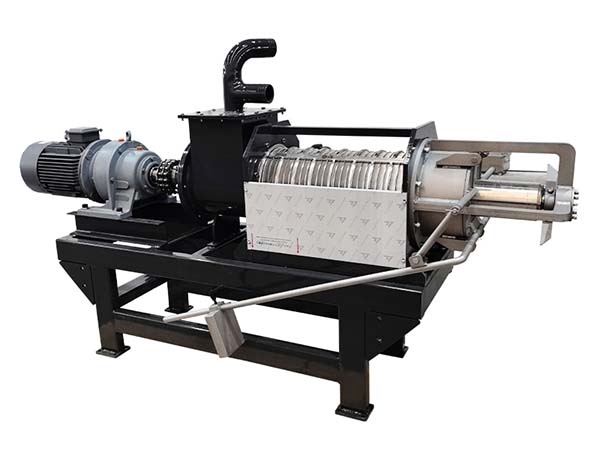
Core Technologies in Horizontal Dewatering
Several proven dewatering technologies operate on a horizontal plane, each excelling in specific applications:
- Screw Press Dewatering Machines: Utilizing a rotating screw within a permeable screen, these machines gradually increase pressure to squeeze liquid out of slurries. Renowned for high dryness, efficient operation, and relatively compact footprints, they are a top choice for municipal sludge, agricultural waste, and certain industrial by-products demanding dry solids output. Continuous operation with manageable energy consumption makes them highly efficient for large volumes.
- Belt Filter Presses: This technology employs a continuous series of rollers pressing sludge sandwiched between two porous belts. Gravity drainage precedes progressively higher pressure zones. Belt Filter Presses excel in high-volume sludge dewatering scenarios, particularly common in municipal wastewater treatment plants. They offer high throughput capacity and effectively handle dilute slurries, delivering consistent cake solid content while maintaining continuous flow.
- Rotary Press Dewatering: Featuring a series of fixed and rotating filtration discs creating pressure zones, Rotary Press machines provide consistent, high-pressure dewatering with typically lower operational noise and vibration. Rotary Press technology shines in applications requiring a stable platform and continuous processing of challenging materials like fibrous waste or biological sludges, often producing drier cakes than some traditional belt presses.
Selecting Your Ideal Horizontal Dewatering Machine
Choosing the best type hinges on a thorough analysis of the application’s specific requirements. Key decision factors include:
- Material Characteristics: Particle size, fiber content, viscosity, abrasiveness, and initial solids concentration significantly influence the choice.
- Required Dryness/Cake Solids Content: Different applications demand different moisture levels. Screw presses and rotary presses often achieve higher dryness than basic belt presses.
- Processing Volume (Throughput): High-volume operations typically lean towards continuous systems like Belt Filter Presses or large Screw Presses.
- Operation and Maintenance Needs: Consider desired automation levels, ease of cleaning, daily maintenance routines, and component lifespan.
- Footprint Constraints: Available space dictates suitable machine sizes; screw presses are often advantageous where space is limited.
- Energy Efficiency Goals: Different technologies have varying power consumption profiles impacting operational costs.
For Voluminous Municipal or Industrial Sludge: Belt Filter Presses remain a dominant, reliable workhorse, known for robust throughput capabilities. Modern designs incorporate enhanced control systems and reduced polymer consumption.
For Demanding Dryness Targets & Energy Efficiency: Advanced Screw Press technology offers compelling results. Innovations have minimized maintenance requirements while maximizing dryness and reducing power usage, making them suitable for diverse materials from food waste to minerals.
For Consistent, Low-Vibration Processing of Challenging Materials: Rotary Press Dewaterers are frequently selected for their steady performance, producing consistently drier solids, particularly beneficial for biosolids and digestates.
Finding the Optimal Fit for Operational Excellence
The modern industrial landscape offers sophisticated horizontal dewatering solutions. There is no universally “best” machine, only the best solution for a specific material and process requirement. Investing time in understanding the characteristics of the slurry to be dewatered and defining clear objectives regarding throughput, dryness, maintenance philosophy, and energy use is paramount.
Consulting with experienced equipment manufacturers and requesting material testing services provides invaluable insights. Many manufacturers offer pilot-scale testing, allowing operators to see real-world performance data on their specific material before making a major capital investment.
Carefully evaluating the different technologies against operational priorities ensures the selected Industrial Horizontal Dewatering Machine delivers optimal results, enhancing efficiency, reducing disposal costs, and contributing to sustainable operation.