Industrial centrifugal dewatering machines are indispensable across numerous sectors, including wastewater treatment, chemical processing, mining, and food production. Their efficiency in separating solids from liquids makes them critical assets. However, unexpected downtime due to operational issues can significantly impact productivity. Proactively addressing common problems ensures consistent performance and maximizes return on investment. This overview highlights five frequent issues encountered with these machines and offers practical solutions for rapid troubleshooting.
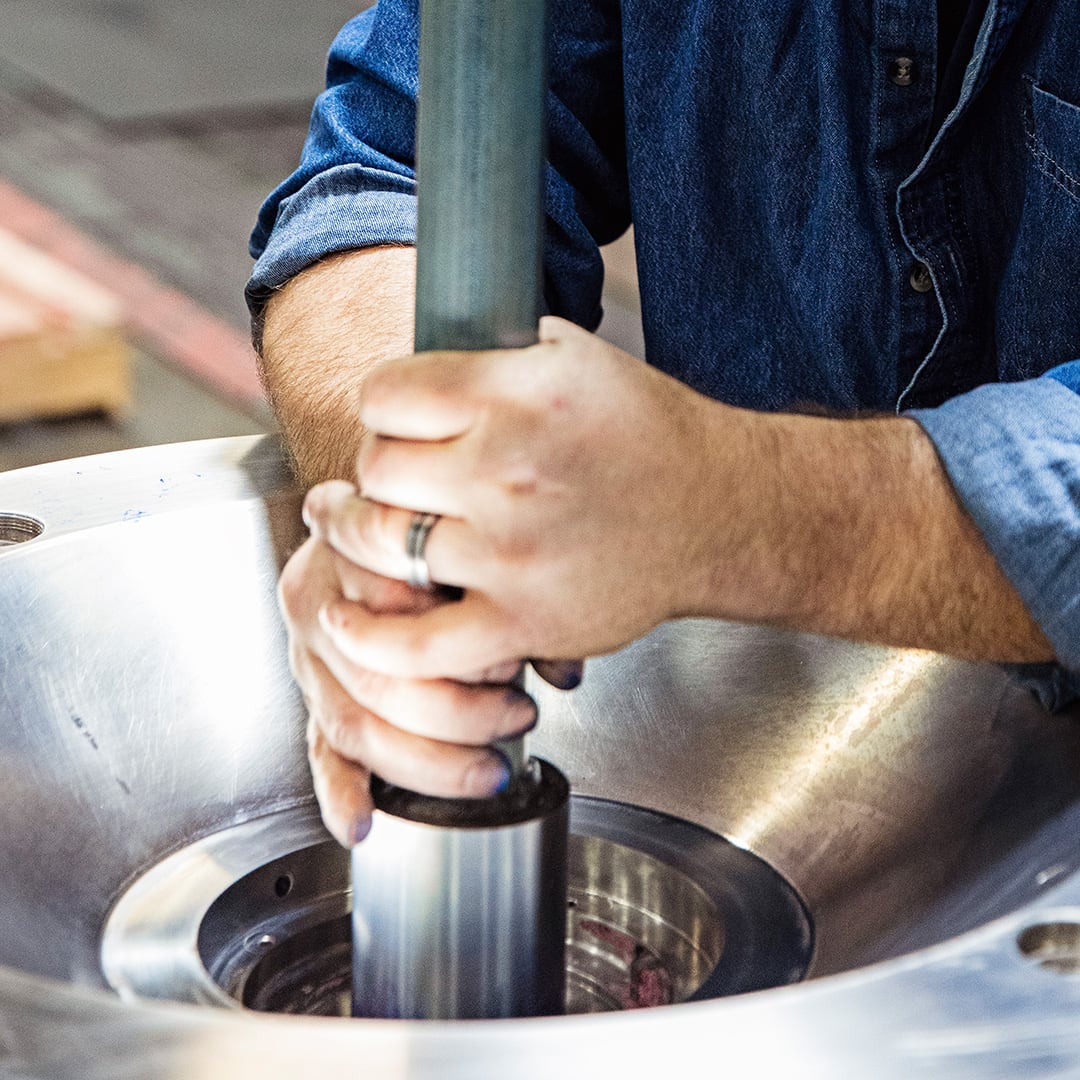
Excessive Vibration During Operation
One of the most frequent and noticeable problems is severe vibration. This can lead to accelerated wear, damage to bearings, and even structural harm to the machine or surrounding equipment.
-
Causes & Solutions:
- Imbalance: Unbalanced loading, whether uneven distribution of feed material across the basket or imbalance within the rotating assembly itself, is a primary cause. Solution: Ensure the feed is distributed evenly and consistently. Regularly check the basket for accumulated solids adhering to one side, performing cleaning cycles as per manufacturer guidelines. For internal imbalance, professional recalibration of the rotor and basket assembly is often required.
- Worn Bearings or Damaged Spindles: Bearings under excessive load or reaching the end of their service life will cause vibration. Spindle damage is more severe. Solution: Incorporate regular bearing inspection into maintenance schedules, listening for unusual noises and feeling for excessive heat. Replace worn bearings promptly using manufacturer-specified parts. Suspected spindle damage necessitates immediate shutdown and expert assessment.
- Foundation Issues: A poorly levelled or inadequately supported machine base will vibrate excessively. Solution: Verify the machine is properly levelled on a solid foundation according to installation specifications. Secure all mounting bolts.
Inefficient Dewatering Performance
When the centrifuge fails to achieve the desired cake dryness or clarity of the centrate, its core function is compromised, potentially affecting downstream processes.
-
Causes & Solutions:
- Improper Bowl Speed: Running below the optimal RPM reduces the G-force needed for effective separation. Solution: Confirm the machine is operating at the correct rotational speed specified for the material being processed. Check drive motor and VFD settings.
- Feed Rate or Concentration Issues: Overfeeding the centrifuge overwhelms its separation capacity. Conversely, highly dilute feed can also hamper effective compaction. Solution: Optimize and strictly control the feed rate according to the machine’s capacity and the specific characteristics of the sludge or slurry. Adjust upstream processes if feed consistency varies unexpectedly.
- Worn or Damaged Conveyor (Decanter Types): A damaged scroll, worn flights, or incorrect differential speed can compromise solids transport and discharge efficiency. Solution: Inspect the conveyor scroll for wear or damage, particularly at critical contact points. Adjust differential speed settings as per operating manuals.
Unusual or Increased Operating Noise
A distinct change in operational noise often signals developing problems requiring immediate attention to prevent catastrophic failure.
-
Causes & Solutions:
- Lack of Lubrication: Bearings running dry generate significant grinding or whining noises. Solution: Adhere strictly to lubrication schedules recommended by the manufacturer. Regularly check lubricant levels and quality.
- Bearing Failure: Advancing bearing failure often produces rumbling, clicking, or grinding sounds. Solution: Immediate shutdown is crucial upon detecting these noises to inspect and replace failing bearings.
- Foreign Object Damage: Impact noises might indicate something hard has entered the centrifuge basket, damaging the scroll or bowl. Solution: Install adequate upstream screening to prevent tramp metal or rocks from entering the machine. Investigate and clear any suspected internal obstructions safely if unusual impacts are heard.
Electrical Issues & Motor Faults
Electrical problems can range from nuisance trips to complete motor failure, halting operations.
-
Causes & Solutions:
- Overload Trips: These often result from jamming, excessive solids loading, or motor strain due to other mechanical faults like failing bearings. Solution: Clear any jams safely. Investigate and rectify the root cause of the overload (e.g., excessive feed rate, mechanical resistance). Ensure starter settings are correct.
- Control Panel Faults: Failures in VFDs, PLCs, or sensors disrupt control. Solution: Reset the system following safe procedures per the operating manual. Diagnose error codes displayed on the control panel. Check sensor connections and functionality. Complex electrical diagnostics may require specialized technicians.
Seal Leakages
Leaks around shaft seals result in environmental contamination, safety hazards, and loss of valuable process fluids.
-
Causes & Solutions:
- Worn/Damaged Seals: Seals degrade over time due to friction, heat, and chemical exposure. Solution: Implement a preventive maintenance plan for regular seal inspection and replacement before failure occurs. Use seals compatible with the processed material.
- Excessive Pressure or Temperature: Operating beyond design limits stresses seals. Solution: Verify process conditions (pressure, temperature) are within the machine’s design specifications. Investigate causes of any abnormal spikes.
- Improper Installation: Incorrectly fitted seals won’t function correctly. Solution: Ensure seals are installed meticulously according to manufacturer procedures.
Prompt identification and resolution of these five common centrifugal dewatering machine issues—excessive vibration, poor separation, unusual noise, electrical faults, and seal leaks—are vital for sustained operational efficiency and minimizing costly downtime. Adherence to rigorous, proactive maintenance protocols, combined with vigilant operator monitoring, significantly reduces the likelihood of such problems arising. When issues do occur, methodical troubleshooting based on these guidelines enables faster recovery, safeguarding productivity and extending the service life of these critical industrial assets.