Mastering the operation of a lotus paste double-auger filling machine is crucial for bakeries and food manufacturers aiming for consistent quality and efficient production. These machines excel at handling dense, sticky pastes like lotus seed paste, offering precision and reliability.
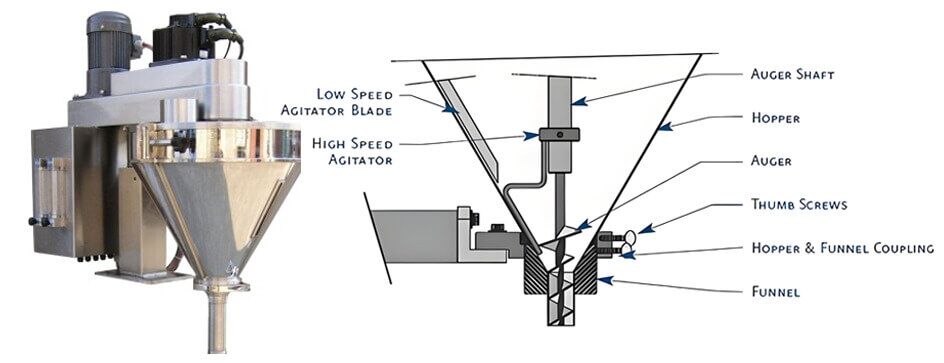
Preparing for Operation
Thorough preparation is the cornerstone of smooth operation. Begin by ensuring the lotus paste has the correct consistency. Extreme temperature variations can negatively impact viscosity; maintaining a cool, stable environment for the paste prior to filling aids flow and metering accuracy.
Assemble the machine according to the manufacturer’s manual. Double-check that all components, particularly the hopper, augers, piston cylinders (if applicable), nozzles, and seals, are clean, correctly installed, and securely fastened. Ensure an adequate supply of containers are ready on the conveyor line.
The Filling Process: Key Steps and Parameters
Initial setup involves critical parameter configuration:
- Paste Temperature: Verify the paste is within the recommended temperature range. Paste that is too warm becomes overly fluid, while paste that is too cold becomes excessively thick.
- Auger Speed: Set the auger rotation speed appropriate for the desired fill volume and paste viscosity. Higher speeds generally increase output rate but require fine-tuning to prevent aeration or uneven filling.
- Fill Volume/Piston Stroke: Precisely set the target fill weight or volume using the machine’s control system. Calibrate using sample fills and scales to achieve exact specifications.
- Nozzle Height: Adjust the height above the container to minimize dripping and splashing. Proximity is key, but ensure it doesn’t touch the container rim.
Initiate a slow start, gradually increasing the speed while monitoring paste flow consistency and fill accuracy. Observe the interaction between the counter-rotating augers as they gently draw paste into the delivery system; consistent movement indicates proper feed. Pay close attention to the weight checks; minor adjustments may be necessary after initial fills to perfect the volume. Continuously monitor for smooth paste flow into containers, avoiding overfilling or underfilling.
Maintaining Efficiency and Quality
Consistent vigilance throughout the production run ensures sustained performance. Periodically re-check fill weights to detect any drift in accuracy, which might suggest changing paste viscosity or minor seal wear. Monitor the paste level in the hopper – maintaining an adequate level prevents air pockets from being drawn into the augers, which can cause inconsistent filling or voids. Regularly observe the filling action for drips, splashes, or uneven dispensing. Address minor issues immediately to prevent larger problems or line stoppages. Maintaining a clean workspace around the nozzles prevents paste buildup that could contaminate containers or disrupt the filling path.
Essential Post-Operation Procedures
Immediately after the run completes, thorough cleaning becomes paramount. Begin by emptying any remaining paste from the hopper using designated tools (never hands!). Follow the manufacturer’s approved cleaning protocols. This typically involves disassembling key components like the hopper, augers, pistons, nozzles, and any tubes or valves that contact the paste. Clean all parts meticulously using appropriate food-grade cleaning solutions, brushes, and cloths. Pay special attention to crevices and seals where paste can accumulate and harden. Rinse thoroughly with clean water to remove all detergent residues. Ensure all parts are completely dry before reassembly to prevent microbial growth. Regular lubrication of designated moving parts, as specified in the manual, is essential for longevity and smooth operation. Store components safely and reassemble the machine for the next run or store it disassembled appropriately.
Troubleshooting Common Issues
Promptly identifying and addressing common problems minimizes downtime:
- Inconsistent Fill Volume: Often caused by fluctuating paste viscosity (check temperature), air bubbles in the paste supply, low hopper level, or worn seals/piston cups.
- Paste Dripping: Can result from incorrect nozzle height, sticky paste residue on the nozzle tip, excessively high paste temperature, or slow nozzle closing speed settings.
- Machine Noise/Vibration: May indicate loose components, lack of lubrication, or misalignment requiring immediate shutdown and inspection.
- Paste Jamming: Usually occurs if the paste is too cold/thick, if foreign objects enter the hopper, or if the auger speeds are incorrectly set.
- Aerated Paste (Frothing): Generally caused by paste feeding too slowly into the augers relative to their rotation speed or excessive air incorporation during paste preparation/handling.
Benefits of Proficiency
Operating the lotus paste double-auger filler efficiently unlocks significant advantages. Precise fill control minimizes waste of valuable ingredients, lowering production costs. Consistent portioning guarantees uniform product quality and weight compliance, meeting stringent standards. Optimized machine speeds significantly increase throughput and overall production line efficiency. Reduced instances of paste jams, drips, or inconsistencies minimizes unplanned downtime for cleaning and adjustments. Furthermore, proactive maintenance and troubleshooting extend the lifespan of the equipment and ensure smooth, trouble-free production cycles. Adhering to meticulous cleaning routines ensures compliance with rigorous food safety regulations.
Competence in operating the double-auger filling machine transforms it from a complex piece of equipment into a reliable asset for high-quality lotus paste production. Focus on thorough setup, precise parameter control, vigilant monitoring, diligent cleaning, and swift issue resolution are the keys to achieving consistently smooth and productive processing runs.