Selecting the right vacuum roller mill is a critical decision for businesses relying on efficient powder processing. When evaluating options in the popular 500 series size category, thorough research and consideration of specific factors are paramount. Here are top tips to guide buyers towards an optimal choice:
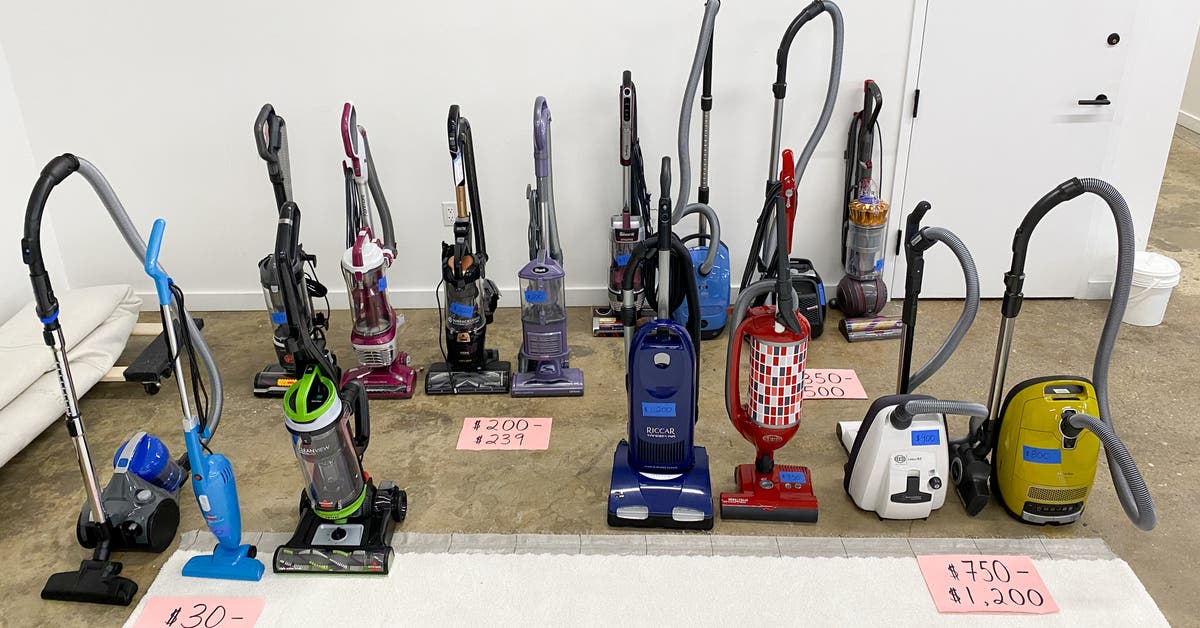
Understanding Your Processing Needs
Before diving into specifications, clearly define your application requirements. The 500 vacuum roller mill designation typically refers to the size and power class, suitable for various industrial tasks. Key questions to ask include:
- Primary Material Properties: What is the hardness, moisture content, particle size distribution, and abrasiveness of the material being processed?
- Desired Output Fineness: What specific particle size range (e.g., D97) is required for your downstream processes or final product?
- Required Throughput Capacity: How much material (e.g., kg/hour) needs to be processed consistently?
- Batch vs. Continuous Operation: Does your process demand continuous feeding or discrete batch processing?
Aligning mill capabilities with these core operational needs is the foundation of a good decision.
Evaluating Key Technical Specifications
Armed with your requirements, scrutinize the technical details of potential 500 vacuum roller mill models:
- Roller Design & Material: Investigate the roller type (e.g., solid, layered), diameter, width, and the alloy composition. Hardness and wear resistance are critical for longevity, especially with abrasive materials.
- Grinding Force and Pressure: Sufficient grinding pressure is essential for achieving fine particle sizes. Understand how the mill generates and regulates grinding force.
- Classifier Efficiency: The integrated classifier determines the final particle size distribution. Look for advanced classifier designs (dynamic or static) offering sharp separation cuts and high efficiency to avoid over-grinding and ensure energy isn’t wasted processing particles already at target size.
- Vacuum System Performance: Effective vacuum is crucial for material feeding, cooling during grinding, dust containment, and conveying the product. Assess the power and efficiency of the vacuum system relative to the mill size.
- Drive Power & Motor Quality: The main motor drives the grinding rollers. Adequate power (kW) is necessary for performance under load. Consider motor efficiency ratings and reliability.
- Construction Quality & Sealing: Examine the overall build quality, materials used in the housing, and the robustness of sealing mechanisms. This impacts dust containment, operational safety (ATEX if applicable), and minimizes maintenance.
Prioritizing Efficiency and Control
Operational costs are heavily influenced by efficiency and control capabilities:
- Energy Consumption: Compare energy consumption data (kWh/tonne) for similar applications. Efficient designs incorporating optimized air flow and drive systems offer significant long-term savings.
- Control System Sophistication: Modern mills feature sophisticated PLC controls. Look for user-friendly interfaces allowing precise adjustment of parameters like roller pressure, classifier speed, and feed rate, often including data logging and recipe management.
- Automation Features: Consider features that enhance automation, such as integrated weighing, remote monitoring capabilities, or automatic gap adjustment, to improve consistency and reduce manual intervention.
Safety and Environmental Compliance
Safety is non-negotiable:
- Explosion Protection (ATEX/DSEAR): If processing combustible dusts, confirm the mill meets stringent ATEX zone requirements or equivalent standards in your region. This includes design features like pressure-shock resistant construction, suppression systems, and grounding.
- Dust Containment: Evaluate the effectiveness of sealing systems to prevent dust emissions during operation and maintenance.
- Ergonomic Design: Consider ease and safety of maintenance access points.
Considering Maintenance and Support
Long-term reliability depends on support:
- Wear Parts Availability & Cost: Inquire about the life expectancy of key wear parts (rollers, liners, classifier blades) and ensure they are readily available at reasonable cost.
- Ease of Maintenance: How easy is it to access and replace wear components? Are specialized tools required? Design features like hydraulically swing-open doors or modular components can drastically reduce downtime.
- Manufacturer Reputation & Service: Research the manufacturer’s track record for reliability, technical expertise, and after-sales service. Prompt, knowledgeable support is invaluable. Look for local service engineers if possible.
- Training & Documentation: Assess the quality of operational manuals, availability of training resources for operators and maintenance personnel.
Conducting Practical Evaluations
Whenever possible, move beyond specifications:
- Request References: Ask the supplier for contact information of customers using the same model for similar applications.
- Seek Material Testing: Provide your specific material sample and request trial runs at the supplier’s facility or another user site. This is the best way to validate performance regarding output fineness, throughput, and energy consumption.
- Factory Visits: If feasible, visit the manufacturing plant to assess build quality processes firsthand.
Making the Final Decision
Compile your findings:
- Total Cost of Ownership (TCO): Look beyond the initial purchase price. Factor in projected energy costs, wear part replacements, maintenance labor, and potential downtime costs over the machine’s expected lifespan. The most reliable and efficient mill often offers the best value long-term.
- Future-Proofing: Consider if the mill can handle potential future material variations or capacity increases.
- Alignment with Core Needs: Ensure the chosen mill demonstrably meets the application requirements defined at the start.
Choosing the best 500 vacuum roller mill requires a systematic approach. By diligently following these buyer tips – focusing on application needs, technical specifications, efficiency, safety, support, and practical validation – businesses can make an informed investment that delivers optimal performance, reliability, and value for years to come.