Maintaining brush potato cleaning machines is crucial for farms and processing facilities aiming to maximize efficiency and reduce costly downtime. While these robust machines simplify the task of removing soil and debris from root vegetables like potatoes, carrots, and beets, consistent upkeep is the key to ensuring they operate at peak performance season after season. Adopting straightforward, regular maintenance routines can significantly extend the lifespan of the equipment and safeguard its output quality.
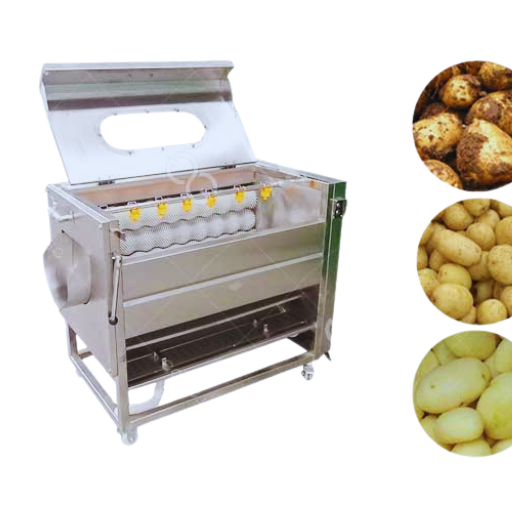
The Importance of Consistent Brush Potato Cleaning Machine Care
Brush potato cleaning machines employ rotating brushes, water sprays, and often vibration to effectively clean produce. Continuous exposure to dirt, grit, water, and vegetable matter subjects components to considerable wear. Neglecting maintenance can lead to premature brush deterioration, reduced cleaning efficiency, motor strain, clogged nozzles, and unexpected breakdowns. Proactive care minimizes these risks, ensuring consistent cleaning performance and protecting the investment.
Essential Maintenance Steps for Optimal Performance
Implementing these simple, scheduled maintenance practices helps keep brush potato cleaning machines running smoothly:
Daily Tasks (After Each Use)
- Thorough Cleaning: Remove all residual mud, soil, and vegetable debris immediately after operation. Use low-pressure water hoses to avoid forcing debris into bearings or electrical components. Power wash systems may simplify this step.
- Brush Inspection: Visually check bristles for wear, breakage, or excessive bending. Damaged or overly worn sections won’t clean effectively and can scratch produce.
- Spray Bar and Nozzle Check: Run a brief water cycle to confirm all spray nozzles are unclogged and delivering water as intended. Clear any blockages promptly. Check spray bar alignment.
- Motor Inspection: Briefly listen for any unusual noises coming from motors during start-up or operation. Ensure adequate ventilation.
- Debris Guard Cleaning: Remove and clean debris guards and collection trays, ensuring no obstructions impede vegetable flow.
Weekly/Monthly Tasks (Depending on Usage Intensity)
- Lubrication: Consult the machine’s manual for specific bearing and gearbox lubrication points and intervals. Apply the recommended lubricant sparingly to prevent attracting more dirt.
- Bearing Inspection: Grasp pulley rims and attempt to rock them; excessive play indicates worn bearings needing replacement. Listen for grinding noises.
- Brush Condition Assessment: Perform a more detailed check of brush bristles. Rotate brush positions if possible to ensure even wear distribution across all brushes.
- Drive Belt Tension: Check the tension of drive belts. Belts that are too loose can slip, causing poor performance and excess heat; belts that are too tight stress bearings.
- Chain Lubrication (If Applicable): Clean chains lightly if heavily soiled and apply the appropriate chain lubricant as specified.
- Electrical Connection Check: Visually inspect power cords and plugs for damage, especially if exposed to harsh conditions.
Quarterly/Annual Tasks
- Brush Replacement: Plan for brush rotation or replacement based on wear patterns and performance. Keep spare brushes readily available.
- Detailed Bearing Service: Consider bearing replacement for high-wear points on a preventive schedule. Replace seals as necessary.
- Full System Flush: Thoroughly clean internal components and flush the water system to prevent scale or mineral buildup.
- Structural Inspection: Examine the frame, hopper, and discharge chutes for cracks, rust, or fatigue, repairing as needed.
- Comprehensive Gearbox Check: Inspect oil levels in gear reducers and change oil according to manufacturer recommendations.
Maximizing Machine Longevity
Beyond scheduled tasks, operator habits significantly impact longevity. Ensure operators are trained in correct procedures and understand the importance of:
- Proper Loading: Avoid overloading the machine, which increases stress on components.
- Managing Foreign Objects: Prevent stones, clumps of clay, or stray tools from entering the machine to avoid severe damage.
- Following Manual Guidelines: Adhere strictly to the manufacturer’s operating instructions and maintenance schedule.
Benefits of Proactive Maintenance
Investing time in consistent maintenance yields substantial returns:
- Reduced Downtime: Fewer unexpected breakdowns mean more productive operating hours.
- Lower Repair Costs: Small, regular checks prevent expensive major component failures.
- Consistent Cleaning Quality: Well-maintained brushes and spray systems ensure reliably clean produce.
- Extended Equipment Lifespan: Proper care maximizes the return on the machinery investment.
- Energy Efficiency: Machines running with correct tension and lubrication operate more efficiently.
Ultimately, treating a brush potato cleaning machine to routine, attentive maintenance transforms it from a potential operational headache into a reliable workhorse. Establishing and adhering to a structured maintenance program focused on brushes, bearings, water systems, and moving parts provides assurance of consistent performance, minimizes repair expenses, and extends the serviceable life of this vital piece of agricultural and food processing equipment. A little scheduled care translates into significant long-term operational benefits.