In the demanding landscape of food processing, maintaining consistent, high-volume output while ensuring product integrity is paramount. For manufacturers specializing in chestnut-based products – from purees and fillings to confectionery items – the efficiency of the filling process directly impacts operational smoothness and bottom-line results. The integration of advanced equipment becomes a strategic decision. Among the specialized machinery options, double-auger chestnut filling machines have gained significant recognition within the industry.
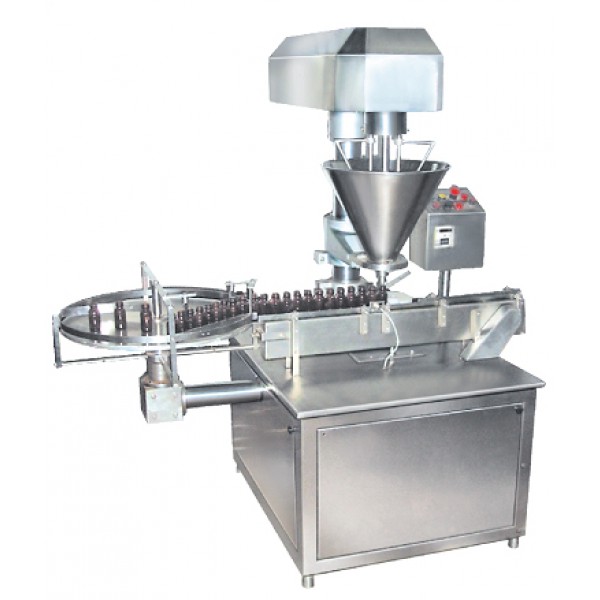
The Imperative of Smooth Operation in Chestnut Processing
Chestnuts, particularly when processed into fillings for pastries, chocolates, or other goods, present unique handling challenges. Their texture requires careful treatment to achieve the desired consistency without over-processing. Manual filling methods or less sophisticated equipment often lead to bottlenecks, inconsistent portioning, product damage (like unwanted crushing), and sanitation difficulties. Downtime for cleaning, frequent maintenance, or troubleshooting erratic performance disrupts production schedules, leading to increased costs and potential waste. Therefore, selecting a filling solution designed explicitly for these challenges is critical for uninterrupted, efficient operations.
Understanding the Double-Auger Advantage
Double-auger chestnut filling machines operate on a principle specifically tailored to handle viscous, chunky, or delicate products like chestnut filling effectively. Two precision-engineered augers, often running in parallel within a hopper or cylinder, work cooperatively:
- Gentle Conveyance: The augers rotate, typically at controlled speeds, gently moving the filling towards the filling heads.
- Improved Flow: This dual-action effectively breaks up any potential clumps or bridges that can form within sticky fillings, ensuring a constant, uniform flow.
- Accurate Metering: The coordinated rotation provides superior control over the volume of product dispensed with each stroke or cycle. This results in highly consistent portioning weights.
- Reduced Shear Stress: Compared to single-auger or piston systems working with similar textures, the double-auger mechanism typically applies less disruptive force to the product, preserving the integrity of chestnut pieces within the filling.
Key Features Defining the Best Choice for Industrial Use
Identifying the optimal double-auger chestnut filling machine requires attention to several critical attributes that contribute to operational smoothness:
- Robust Construction & Hygiene Focus: Industrial environments demand durable materials like stainless steel (especially 304 or 316 grades) for all contact parts. Easy disassembly for thorough cleaning and sanitation (CIP/SIP compatibility as needed) is non-negotiable to meet stringent food safety standards and minimize downtime.
- Precision Control Systems: Advanced microprocessor controls allow operators to finely tune parameters such as auger speed, fill volume, and timing cycles. Digital interfaces simplify operation, recipe storage, and provide diagnostics for troubleshooting.
- Adaptable Filling Heads: Versatility is key. The machine should seamlessly integrate various nozzle sizes and possibly interchangeable piston/cylinder units to handle different chestnut filling consistencies and container sizes, from small pastry cavities to larger jars or tubs.
- Minimal Maintenance Design: Reliable performance necessitates accessible components and proven auger/drive mechanics that minimize the frequency and complexity of maintenance tasks. Seals and bearings should be food-grade and durable.
- Speed and Efficiency: Production throughput must align with the facility’s output targets. High-quality double-auger units provide efficient filling cycles without compromising on portioning accuracy, contributing directly to meeting production quotas.
- Operator Ergonomics & Safety: Well-designed machines prioritize operator safety with proper guarding and emergency stops, while also considering ease of loading material, changing components, and monitoring the process to reduce fatigue.
Impact on Industrial Operations
The tangible benefits of deploying a well-chosen double-auger chestnut filling machine manifest across the production line:
- Enhanced Productivity: Consistent, rapid, and automated filling significantly increases output volume compared to manual or less efficient automated methods.
- Superior Product Consistency & Quality: Precise portion control ensures uniformity across all batches, while gentle handling preserves the aesthetic appeal (chunk retention) and textural quality of the chestnut filling, enhancing consumer satisfaction.
- Reduced Product Waste: Accurate filling minimizes overfilling, and the gentle action reduces product damage during the filling process.
- Optimized Labor Utilization: Automation of the filling task allows skilled operators to focus on supervision, quality control, or other value-added tasks.
- Downtime Minimization: Reliable performance and ease of cleaning/maintenance translate into fewer operational interruptions.
- Compliance Assurance: Hygienic design facilitates adherence to GMP and food safety regulations.
Selecting the Optimal Partner
Making the best choice involves thorough evaluation beyond basic specifications. Production managers should assess:
- Reputable Suppliers: Partnering with established manufacturers known for quality engineering and robust after-sales support (training, readily available spare parts, technical assistance) is crucial.
- Specific Production Parameters: Clearly define requirements regarding filling speed, accuracy tolerances, desired throughput, product characteristics (viscosity, chunk size), and container types.
- Validation & Testing: Requesting product trials using the actual chestnut filling is highly recommended to witness performance firsthand before finalizing the purchase.
Choosing the right double-auger chestnut filling machine is an investment directly impacting the smoothness and profitability of industrial processing lines. Prioritizing robustness, precision control, hygiene, adaptability, and reliability ensures this critical piece of equipment consistently delivers optimal performance, safeguarding product quality and driving operational efficiency for manufacturers in the chestnut product sector.