Maintaining industrial equipment efficiently can significantly impact operational longevity and productivity. For facilities utilizing vacuum roller machines, implementing a structured maintenance routine proves crucial to maximizing service life. The following four-step approach offers a practical framework.
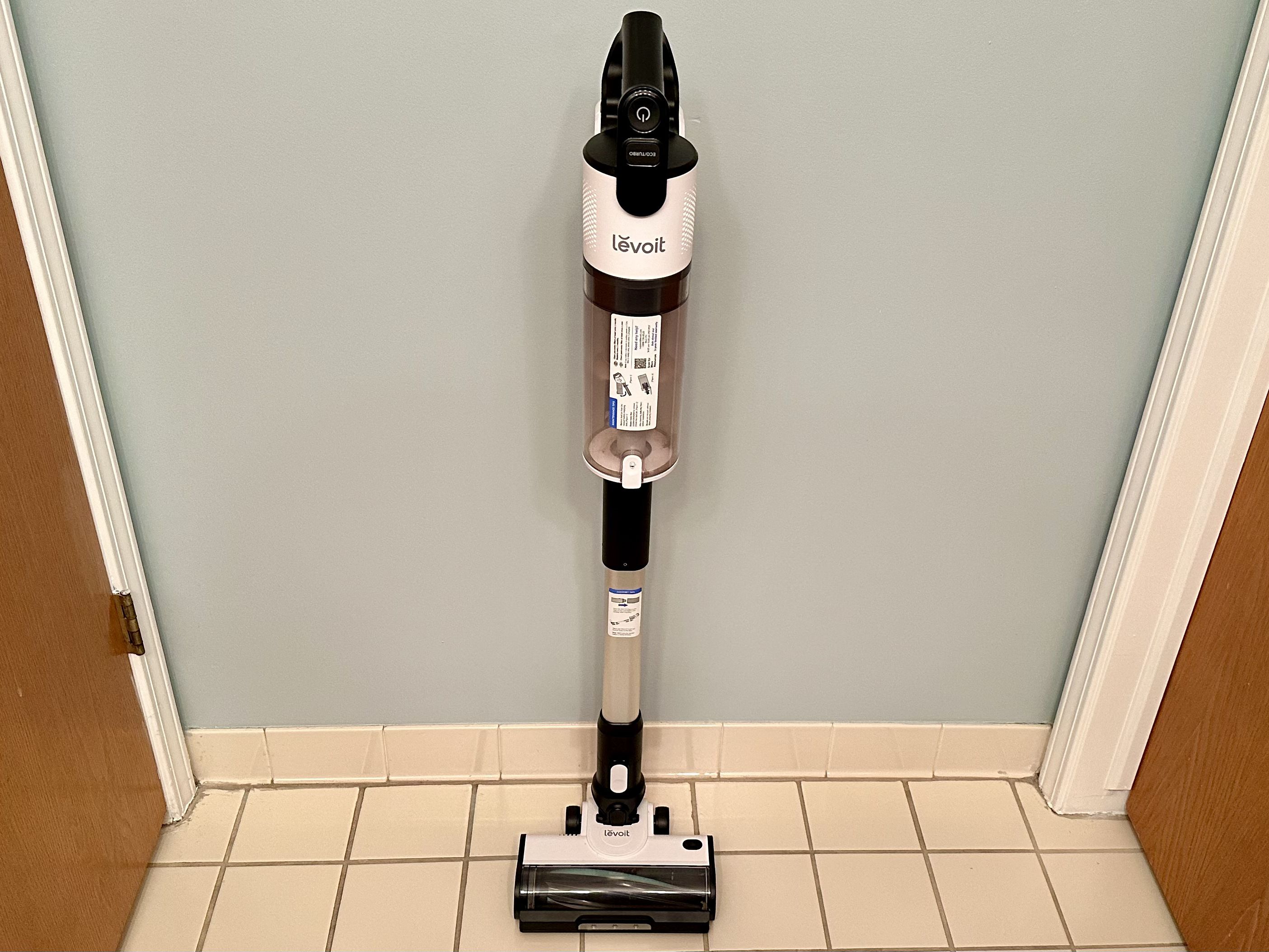
Step 1: Consistent Cleaning Protocols
Dust, debris, and adhesive residue accumulation pose significant threats to vacuum roller functionality. Establishing a strict daily cleaning routine is paramount. Operators should focus on the roller surface, vacuum ports, and surrounding collection chambers using recommended non-abrasive tools and approved cleaning agents. Immediate attention to spillages prevents hardening and potential damage to sealing surfaces. Consistent cleaning prevents unnecessary strain on motor bearings and maintains optimal suction efficiency.
Step 2: Thorough Inspection & Lubrication
Regular inspections identify wear before it leads to failure. Weekly visual and operational checks should cover:
- Roller Surface Integrity: Inspect for scratches, dents, or uneven wear affecting material handling.
- Bearings & Drive Components: Check for unusual noise, heat, or play indicating bearing wear.
- Belts & Chains: Examine tension and condition for signs of fraying or stretching.
- Electrical Connections: Ensure terminals are tight and free from corrosion.
Following inspection, apply manufacturer-specified lubricants precisely to designated points like bearings and drive mechanisms, adhering strictly to recommended intervals and quantities. Over-lubrication can be as detrimental as neglect.
Step 3: Calibration and Performance Verification
Optimal machine performance relies on precise settings degrading over time. Schedule monthly calibration checks focusing on:
- Vacuum Pressure: Verify pressure levels meet operational requirements using calibrated gauges.
- Roller Speed & Alignment: Ensure consistent speed settings and that rollers are perfectly parallel.
- Sensors & Controls: Test limit switches, pressure sensors, and emergency stops for accurate function.
Documentation of calibration results helps track performance trends and facilitates targeted adjustments.
Step 4: Proactive Parts Replacement
Component wear is inevitable. A proactive approach involves replacing critical wear parts before catastrophic failure occurs, based on manufacturer guidelines and operational history tracked through maintenance logs. Key components typically requiring scheduled replacement include:
- Drive belts and chains
- Motor brushes (where applicable)
- Filters and sealing gaskets
- High-friction bearings
- Worn roller surfaces or covers
Maintaining an inventory of essential spares minimizes costly production downtime during replacements.
The Result: Enhanced Longevity and Reliability
Diligent adherence to these four steps—consistent cleaning, thorough inspection/lubrication, regular calibration, and proactive parts replacement—creates a robust maintenance culture. This systematic approach directly translates into tangible benefits: minimized unplanned breakdowns, reduced costly emergency repairs, sustained peak operational efficiency, and, critically, significantly extending the productive lifespan of the 200 Vacuum Roller Machine. Consistent maintenance is fundamentally an investment in sustained productivity and long-term operational cost savings.