The potato processing industry continuously seeks efficient solutions to meet production demands while controlling expenses. Machines capable of handling 1500 kg of potatoes per hour represent a significant investment for medium to large-scale operations. Understanding the cost factors and implementing energy-saving strategies are crucial for maximizing the return on investment for such equipment.
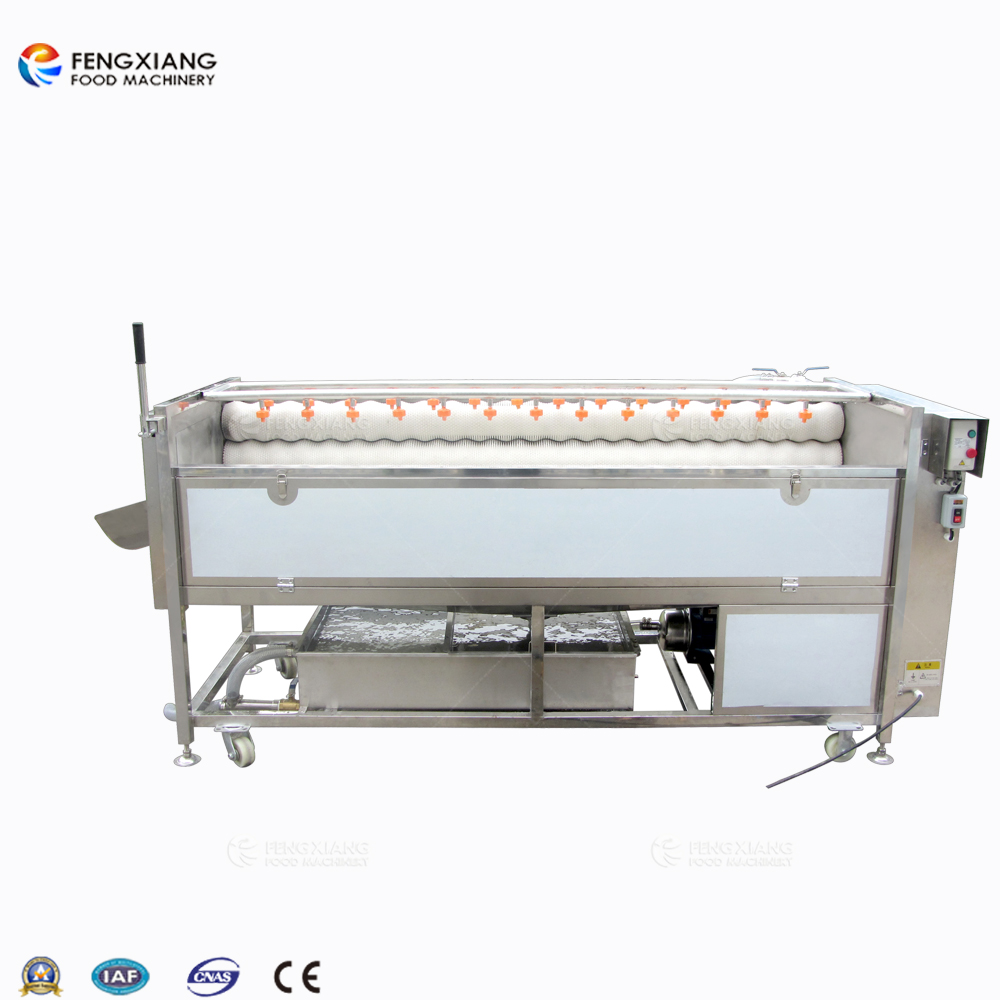
The 1500kg/h Potato Cleaning and Peeling Machine: Core Functionality
Industrial potato cleaning and peeling machines are designed to automate and streamline the initial stages of potato processing. A model rated for 1500 kilograms per hour typically incorporates robust washing mechanisms, such as rotating drums or brush systems, to remove soil and debris. This is often followed by abrasive peeling cylinders or specialized rollers to efficiently remove the potato skin with minimal product loss. These machines significantly reduce manual labor requirements compared to traditional methods, enhancing productivity and improving hygiene standards within processing plants.
Understanding the Cost Factors for a 1500kg/h Unit
The initial purchase price of a 1500kg/h potato cleaning and peeling machine is the most visible cost component. However, a comprehensive financial analysis requires considering several other elements:
- Machine Specifications and Build Quality: Prices vary significantly based on materials (e.g., stainless steel grades), engineering sophistication, automation levels (basic controls vs. advanced PLCs), and the inclusion of features like integrated water filtration or specific peeling technology (abrasive, knife-based, steam).
- Manufacturer and Brand: Established brands often command a premium due to reputation and proven reliability, while newer entrants or less complex models might offer lower upfront costs. Technical support availability and quality should be factored in.
- Installation and Setup: Costs associated with transporting the machine to the facility, installation labor, utility connections (electrical, plumbing), and potential site modifications.
- Operational Costs: This encompasses ongoing expenditure on water, electricity, sanitation chemicals, replacement brushes or abrasives, and routine maintenance parts.
- Maintenance: Regular preventative maintenance is essential for longevity and efficiency, involving costs for inspections, lubrication, and component wear parts.
As a rough industry guideline, prices for a new, solidly constructed 1500kg/h machine often start in the range of several thousand dollars and can increase substantially depending on the factors above. Thorough research and obtaining detailed quotes from multiple reputable manufacturers are essential steps before purchase.
Energy-Saving Strategies for Efficient Operation
Given the substantial water and electricity consumption of industrial food processing machinery, optimizing energy usage is critical for long-term cost control and environmental responsibility. Here are practical tips for operating a 1500kg/h potato cleaning and peeling machine efficiently:
- Water Management and Recycling: Implement water recycling systems where feasible. Filtration systems allow water to be reused multiple times in the washing stages, drastically reducing fresh water intake and wastewater volume. Ensure leaks are promptly repaired.
- Optimize Loading: Avoid consistently underloading the machine. Running the unit closer to its designed capacity (without exceeding it) ensures the energy and water consumed per kilogram of processed potatoes is minimized.
- Peel Waste Minimization: Machines achieving efficient peeling with minimal flesh loss inherently reduce waste. Ensure the machine is properly calibrated for the potato variety and condition, as over-peeling wastes product and increases the effective energy cost per usable output.
- Energy-Efficient Motors: When selecting a machine or replacing motors, opt for high-efficiency models. While potentially a higher initial cost, they offer significant long-term electricity savings.
- Scheduled Operation: If possible, schedule operation during off-peak electricity rate hours to capitalize on lower energy costs, if your utility provider offers time-of-use billing.
- Preventative Maintenance: A well-maintained machine is an efficient machine. Clean components regularly, ensure bearings are lubricated, belts are tensioned correctly, and abrasive surfaces are replaced before excessive wear reduces efficiency and increases motor load.
- Employee Training: Ensure operators are fully trained on the machine’s efficient operation, including correct loading procedures, proper settings for different potato batches, and awareness of water and energy consumption metrics.
Conclusion: Balancing Investment and Efficiency
Investing in a 1500kg/h potato cleaning and peeling machine requires careful consideration of both the initial capital outlay and the ongoing operational expenses. By understanding the various cost components – from the base price and installation to long-term water and energy consumption – processors can make informed purchasing decisions. Furthermore, diligently applying energy-saving practices, particularly focusing on water recycling/reduction, optimal loading, peel waste control, and preventative maintenance, directly translates into substantial cost reductions over the machine’s operational lifespan. This combination of smart investment and operational efficiency enables businesses to enhance productivity while effectively managing expenses.