In modern agricultural processing, efficiency and quality control are paramount concerns for potato producers. Equipment that handles substantial volumes while maintaining precision offers significant benefits. The selection of a 1000-potato cleaning and grading machine presents distinct advantages for operations prioritizing scalability and quality. This article outlines three key advantages observed with such systems.
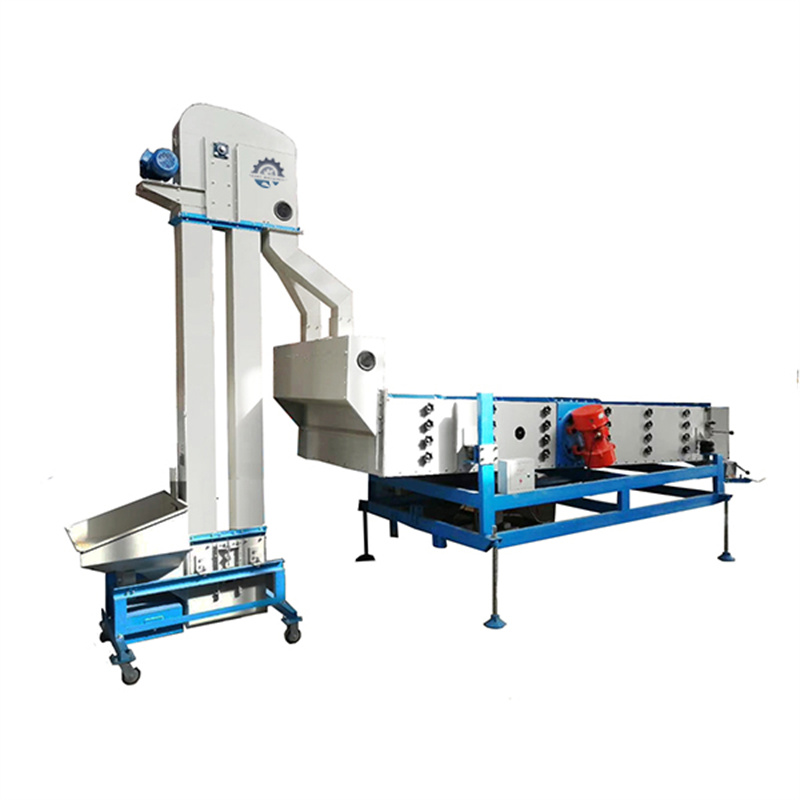
Unmatched Processing Throughput
The primary advantage lies in the substantial processing capacity. A machine designed for simultaneous cleaning and grading of up to 1000 potatoes represents a significant leap in operational efficiency compared to manual sorting or lower-capacity equipment. This high-volume capability ensures producers can handle large harvests or meet continuous production demands without becoming a bottleneck. Such throughput minimizes delays, optimizes the use of subsequent processing lines or storage facilities, and ensures potatoes move swiftly from field to market or storage, maximizing freshness and reducing potential spoilage risks associated with prolonged handling times.
Consistent Quality and Precision Grading
Beyond speed, maintaining consistent quality is non-negotiable. Modern 1000-potato machines utilize advanced mechanisms – often incorporating gentle brush rollers, efficient water spray systems, and sophisticated optical or weight-based sorting technology. This combination delivers several benefits:
- Superior Cleaning: Effective removal of soil, debris, and light imperfections without damaging the potato skin.
- Accurate Grading: Precise sorting by size, weight, and often shape or superficial quality (e.g., removing blemishes) ensures uniform batches tailored to specific market requirements (e.g., retail size standards, processing specifications).
- Reduced Waste: Consistent identification and removal of sub-standard potatoes minimizes waste and ensures only premium tubers proceed for packaging or processing, maximizing usable yield per harvest.
This automation eliminates the subjectivity and fatigue inherent in manual grading, guaranteeing a reliable and standardized output that builds brand reputation for quality.
Significant Labor and Operational Cost Savings
Implementing a high-capacity cleaning and grading machine translates directly into tangible economic benefits:
- Reduced Labor Dependency: Automating the labor-intensive tasks of washing and sorting drastically reduces the workforce required for these processes. This alleviates challenges in finding manual labor and lowers associated payroll costs.
- Lower Water and Energy Consumption: Engineered systems often incorporate water recycling loops and energy-efficient motors, optimizing resource usage compared to less sophisticated equipment or manual methods.
- Minimized Product Loss: Gentle handling mechanisms reduce bruising and damage during the cleaning process, while precise grading ensures optimal product utilization, contributing directly to the bottom line.
- Scalability: The large capacity inherently suits growing operations. It provides room for expansion without the immediate need for further equipment investment, offering a future-proof solution.
Conclusion: A Strategic Investment
For potato producers seeking to enhance efficiency, guarantee consistent quality, and improve their cost structure, investing in a 1000-potato cleaning and grading machine presents a compelling case. The advantages of high-volume throughput, precise and automated quality control, and substantial reductions in labor and operational costs underscore its value proposition. Such equipment is not merely a processing tool; it represents a strategic investment in enhancing productivity, profitability, and the long-term competitiveness of a potato farming or packing operation.