Meat filling frequency conversion choppers are crucial equipment in modern food processing lines, particularly for sausage production or minced meat applications. These complex machines combine mechanical chopping action with sophisticated frequency conversion technology to precisely control motor speed, ensuring consistent filling texture and volume. However, like any industrial machinery, operators can encounter recurring technical issues that disrupt production flow. Understanding the most common problems and their solutions is key to minimizing downtime.
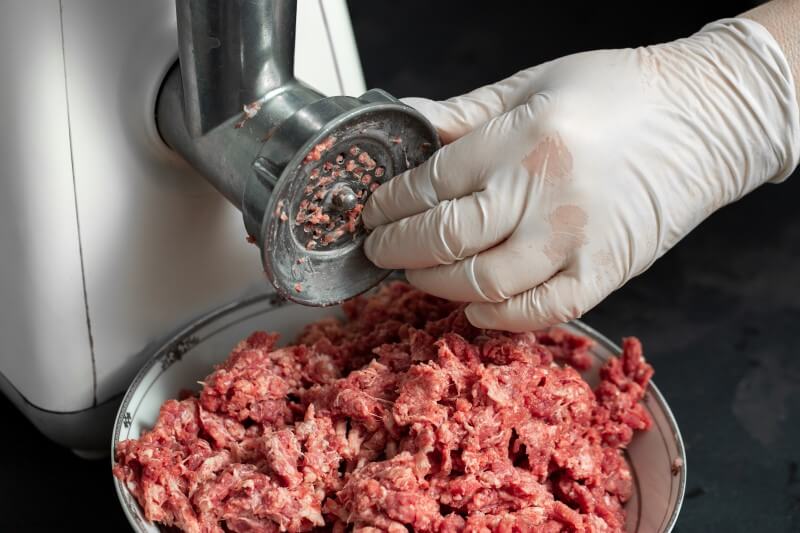
Issue 1: Motor Overheating and Unexpected Shutdowns
One of the most frequent complaints involves the main chopper motor overheating during operation, triggering thermal protection shutdowns. This interrupts the filling process and can potentially damage motor windings if persistent.
- Causes: Often traced to inadequate ventilation around the motor housing, allowing heat buildup. Dust, meat debris, or grease accumulating on cooling fins dramatically reduces heat dissipation efficiency. Overloading the machine beyond its capacity or prolonged operation at very high speeds without breaks also strains the motor. Occasionally, faulty motor bearings causing excess friction can generate significant heat.
- Solutions: Ensure the machine environment is clean and provides sufficient air circulation. Implement a strict cleaning schedule for the motor housing and cooling fins using appropriate compressed air or brushes (following lock-out/tag-out procedures). Verify operators adhere to recommended capacity limits and avoid continuous operation at maximum speed settings for extended periods. Listen for unusual grinding noises from the motor bearings and schedule professional inspection if suspected.
Issue 2: Inconsistent Meat Texture and Choppering Quality
Operators may notice the minced or filled meat output becomes uneven – sometimes too coarse, other times too fine, or showing variations in particle size distribution. This directly impacts product quality and consistency.
- Causes: Dull, damaged, or improperly installed chopper blades are prime suspects. Worn bearings supporting the blade shaft introduce wobble, preventing a clean cut. Irregular feeding speeds caused by upstream equipment issues or operator error can overwhelm the chopper mechanism momentarily. Improperly calibrated frequency converter settings affecting blade speed consistency under variable load can also lead to texture issues.
- Solutions: Institute a rigorous blade inspection and sharpening/replacement program. Check blade bolts for correct torque and ensure blades are aligned correctly. Regularly inspect bearings for wear and replace them proactively. Ensure upstream feeding equipment, like augers or hoppers, operates smoothly and consistently. Review frequency converter parameters and fine-tune settings (potentially requiring a technician) to ensure speed stability during load fluctuations.
Issue 3: Frequency Converter Malfunctions (Fault Codes, Speed Instability)
The frequency converter, responsible for controlling motor speed electronically, can itself malfunction. This manifests as frequent fault codes appearing on its display panel, an inability to reach set speeds, or erratic and uncontrolled motor speed fluctuations.
- Causes: Environmental factors like excessive heat, humidity, or dust accumulation inside the converter cabinet are common culprits. Loose or corroded electrical connections at the converter terminals can cause intermittent faults. Voltage surges or dips from the main power supply can trigger protective shutdowns or damage sensitive electronics. Parameter settings might also become corrupted.
- Solutions: Maintain a clean, cool, and dry environment around the converter cabinet. Regularly power down the system and inspect connections for tightness and signs of corrosion or overheating. Use appropriate protective devices like surge suppressors on the incoming power line. Document and reset fault codes according to the manufacturer’s manual after identifying and addressing the root cause. Ensure converter parameter settings are properly saved and backed up.
Issue 4: Conveyor or Feeding Mechanism Jamming
Problems can also occur with the conveyor or auger feeding meat to the chopper head. Blockages or jams stop the filling process entirely and pose potential safety risks during clearing.
- Causes: Feeding material that contains hard contaminants like bone fragments or gristle. Feeding overly frozen, large, or uneven chunks of meat that exceed the feed opening capacity. Misadjusted feeding speed that doesn’t synchronize well with the chopper’s processing rate. Worn conveyor belts, auger flights, or damaged feed auger bearings.
- Solutions: Implement stringent quality control checks on raw materials to exclude foreign objects and ensure meat trimmings are of appropriate size and temperature (partially thawed if frozen) before feeding. Properly trim large pieces. Adjust conveyor or auger feed speed to match the chopper’s processing capacity smoothly. Regularly inspect and maintain feed mechanisms, replacing worn components like belts, auger sections, or bearings before failure causes a jam.
While these four issues – motor overheating, inconsistent texture, frequency converter faults, and feeding jams – represent common challenges, proactive maintenance and operator training significantly reduce their occurrence. Regular cleaning, thorough inspection schedules for blades and bearings, attention to environmental controls for the electronics, and careful management of feed material consistency are fundamental practices. Addressing these specific problems systematically helps maintain optimal chopper performance, ensuring smooth production runs and consistent, high-quality meat filling output. Swift identification and resolution minimize costly downtime.