Centrifuges represent critical components within chemical processing facilities, facilitating essential separation tasks. The question of longevity—how long a chemical plant centrifuge lasts—naturally arises among plant managers and maintenance engineers seeking optimal equipment performance and return on investment. While design, manufacturer specifications, and operational demands significantly influence lifespan, implementing consistent, proactive maintenance strategies can substantially extend service life and enhance reliability.

Understanding Centrifuge Lifespan Variables
Predicting an exact lifespan for a centrifuge is complex. Various factors interplay to determine how long these machines operate effectively before requiring major overhaul or replacement.
- Operational Environment: Exposure to harsh chemicals, high temperatures, or abrasive particulates accelerates wear and corrosion.
- Duty Cycle: Machines running continuously 24/7 face more stress than those on batch or intermittent schedules.
- Process Conditions: Factors like feed slurry consistency, differential pressures, and vibration levels impact mechanical stress.
- Initial Build Quality: The materials of construction, engineering design, and manufacturing precision set a baseline for longevity.
- Maintenance Regimen: This remains the most significant variable operators can directly influence.
Generally, well-maintained centrifuges in demanding chemical environments can operate effectively for 7 to 15 years or more before major component failure necessitates replacement. However, neglecting basic care can drastically shorten this timeframe to a few years, leading to costly unplanned downtime.
Actionable Steps to Maximize Centrifuge Longevity
Proactive maintenance, not reactive repairs, is key to extending centrifuge life quickly and efficiently. Focusing on these essential practices delivers tangible results:
1. Rigorous Adherence to Lubrication Schedules:
Proper lubrication is paramount for minimizing friction and wear on bearings, gears, and other high-speed rotating components. Follow the manufacturer’s exact specifications for:
- Lubricant type and viscosity grade.
- Correct application points and fill levels.
- Precise relubrication intervals based on runtime hours.
Contamination control during lubrication is crucial. Cleanliness during grease gun use or oil changes prevents introducing damaging particles. Over-lubrication can be as detrimental as under-lubrication, potentially causing overheating.
2. Implementing Robust Vibration Monitoring:
Vibration serves as a primary indicator of developing mechanical issues. Establishing a consistent vibration monitoring program allows for early detection of:
- Bearing wear or failure.
- Imbalance due to uneven cake build-up or rotor damage.
- Misalignment issues.
- Resonance problems.
Regular readings establish baseline data, making deviations easier to spot. Using portable analyzers periodically or installing fixed sensors enables trend analysis and predictive maintenance scheduling, preventing catastrophic failures.
3. Meticulous Cleaning and Inspection Protocols:
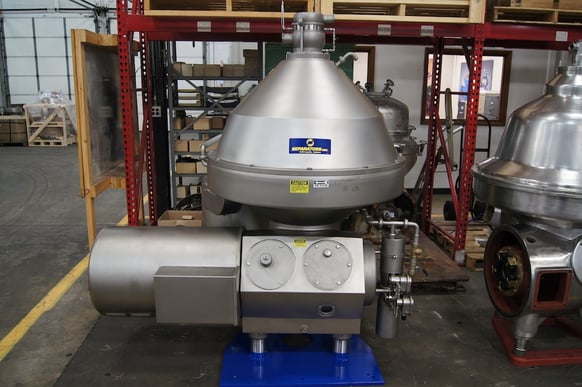
Residual chemical deposits, process scale, or accumulated solids cause corrosion, imbalance, and operational inefficiency. Scheduled, thorough cleaning during planned downtime is non-negotiable. This provides the opportunity for detailed visual inspections:
- Check for signs of corrosion, cracks, or erosion on the bowl, housing, and frame.
- Inspect seals and gaskets for wear, hardening, or leaks.
- Examine belts (if applicable) for tension and signs of wear.
- Ensure fasteners are secure.
Detailed inspection reports track component condition over time, guiding replacement decisions proactively.
4. Training for Proper Operation and Minor Adjustments:
Operator technique significantly influences machine stress. Ensuring personnel are thoroughly trained on:
- Correct start-up and shutdown sequences.
- Achieving and maintaining proper feed rates and load conditions.
- Recognizing early warning signs (unusual noises, leaks, performance shifts).
- Performing specific minor adjustments and daily checks safely.
Empowering operators helps prevent operational errors that strain the machine.
5. Timely Replacement of Wear Components:
Certain components degrade predictably and are designed as replaceable parts. Do not wait for failure:
- Seals and gaskets: Replace per schedule or at signs of leakage.
- Belts: Replace based on inspection findings and manufacturer guidelines.
- Bearing sets: Consider proactive replacement during major overhauls if vibration trends indicate potential wear approaching end-of-life, even if not yet failed.
- O-rings and lip seals.
Proactively replacing these known failure points during planned maintenance windows minimizes unplanned downtime risks.
The Cumulative Impact: Enhanced Reliability and Cost Savings
Implementing these focused steps creates a compounding effect on centrifuge reliability and lifespan. Consistent lubrication prevents premature bearing failure. Vibration monitoring catches imbalance before it damages the spindle. Cleanliness reduces corrosion rates. Proactive wear part replacement avoids secondary damage during failure. Well-trained operators handle the machine correctly.
The result is significantly reduced instances of emergency breakdowns and costly production stoppages. Maintenance shifts from a high-cost, reactive mode to a predictable, planned activity. This not only extends the operational life of the centrifuge, potentially adding years to its service, but also optimizes the total cost of ownership through maximized uptime and controlled maintenance spending.
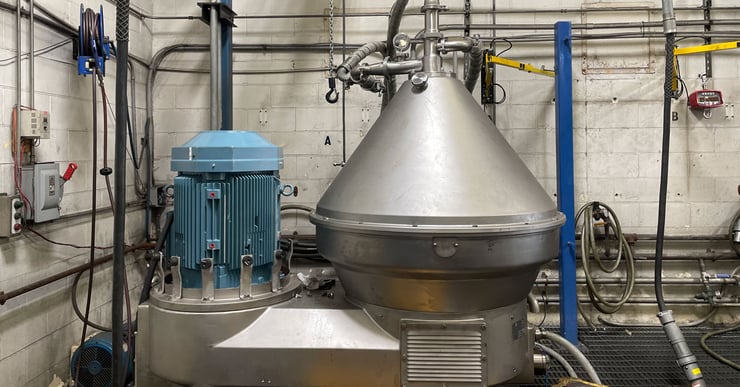
Understanding the factors influencing lifespan and diligently applying these fundamental maintenance practices represents the most direct path to ensuring a chemical plant centrifuge reliably serves its critical function for its maximum potential operational life.