Selecting the Ideal Industrial Horizontal Dewatering Machine: Essential Features Checklist
Procuring an industrial horizontal dewatering machine represents a significant investment for facilities involved in sludge management, be it in municipal wastewater treatment, food processing, pulp & paper, or chemical industries. The right equipment maximizes solids capture, minimizes polymer consumption, reduces operating costs, and ensures smooth, continuous operation. Given the variety of models available, focusing on key technical features during the evaluation process is paramount for making an informed decision.
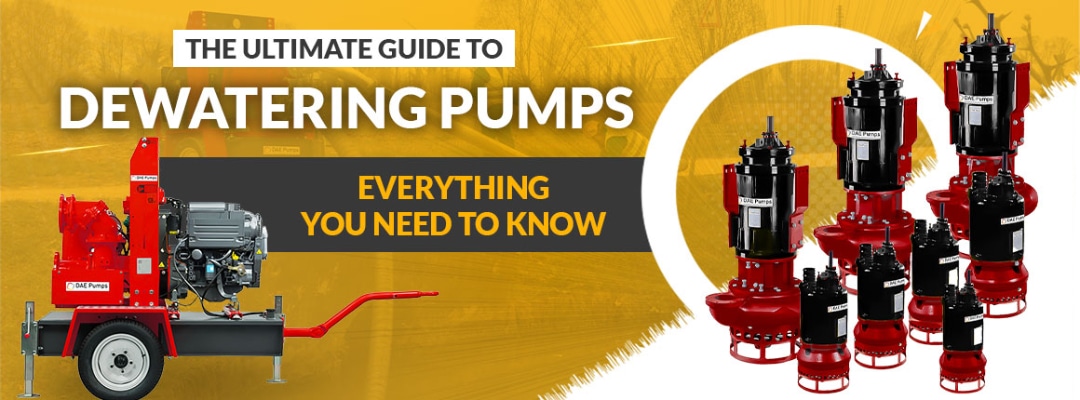
Core Functionality and Machine Construction
Understanding the fundamental design and build quality provides the foundation for assessing a machine’s suitability:
- Frame Construction and Materials: Robust construction using high-grade stainless steel (typically 304 or 316L for harsh environments) is non-negotiable. Look for reinforced structures capable of withstanding significant mechanical stresses and corrosive elements prevalent in sludge handling.
- Deck Layout and Length: The machine’s deck length directly influences residence time and, consequently, cake dryness. Evaluate options based on the specific solids characteristics and target dryness levels required. Variable slope settings offer flexibility.
- Filter Belt Type and Weave: The belt is critical. Consider material (typically polyester or polypropylene monofilament), weave pattern (which affects drainage speed and solids retention), permeability, and resistance to abrasion, clogging, and chemicals. Availability and cost of replacement belts are practical considerations.
- Drainage Zones Configuration: Efficient machines incorporate optimized drainage zones (gravity drainage, wedge zone, low-pressure, high-pressure). Assess how the design promotes rapid water release and progressive dewatering along the belt path.
Drive, Control, and Washing Systems
Operational efficiency and control heavily depend on these components:
- Drive System: Look for independent, variable speed drives for both the main belt and the gravity/pressure rolls. Frequency-controlled drives allow precise adjustment of belt speed to match feed rates and optimize cake formation. Robust gearboxes and motors are essential.
- Comprehensive Control Panel: A modern, user-friendly PLC-based control panel is crucial. Key features include intuitive interfaces for setting and monitoring belt speed, wash water flow, tracking, tension, and potentially polymer dosing integration. Alarms for malfunctions (e.g., belt deviation, low tension) enhance operational safety.
- Effective Belt Washing System: High-pressure wash water systems (both top and bottom showers) are vital to prevent blinding and maintain belt permeability. Ensure sufficient pressure capacity and well-designed nozzles for complete cleaning coverage. Consider water source and recovery options.
- Reliable Belt Tracking Mechanism: Automatic and responsive belt tracking systems (pneumatic or hydraulic) are critical for operational stability and preventing costly belt damage. Manual correction capabilities should also be present.
- Tensioning System: Robust, adjustable belt tensioning ensures proper belt grip on the drive rollers and facilitates effective cake discharge.
Sludge Conditioning and Dewatering Performance
The machine’s capability to handle specific sludge types effectively is the ultimate measure:
- Sludge Feed Distribution: An efficient feed system (like a flume or feed box) ensures even sludge distribution across the full belt width for uniform cake formation and optimal utilization of the belt surface area.
- Polymer Mixing System Integration: While often a separate unit, the interface and compatibility with polymer conditioning systems are critical. The conditioning effectiveness significantly impacts achievable cake dryness and machine throughput.
- Proven Solids Capture Rate: Evaluate performance data for the specific sludge type relevant to your operation. High solids capture (typically >95%) minimizes return loads and environmental impact.
- Achievable Cake Dryness (% Solids): This is a key performance metric impacting disposal costs. Request achievable dryness percentages based on sludge characteristics similar to yours, considering the machine configuration and conditioning.
- Specific Throughput Capacity (kg DS/m belt width/hr): Ensure the machine’s rated capacity aligns with your peak sludge production volumes for the available operating hours.
Operational Maintenance and Support
Long-term reliability and cost-effectiveness depend heavily on these factors:
- Ease of Access for Maintenance: Simple access to bearings, sprays, rollers, and the filter belt streamlines routine inspections and part replacements, reducing downtime.
- Critical Component Quality: Assess the quality and reputation of bearings, seals, spray nozzles, and scraper blades. Higher quality components often mean longer service life.
- Vendor Technical Support & Spares Availability: Investigate the manufacturer’s reputation for technical support response times, field service availability, and the local/regional stock level of essential spare parts. Comprehensive documentation (manuals, parts lists) is essential.
- Operator Safety Features: Guarding for rotating parts, emergency stops, and lock-out/tag-out provisions are mandatory safety requirements.
Conclusion
Selecting an industrial horizontal dewatering machine is a complex process demanding meticulous attention to engineering features and performance data. By systematically evaluating the machine’s construction, drive and control systems, sludge conditioning integration, proven dewatering performance under comparable conditions, and the vendor’s support infrastructure using this essential feature checklist, buyers can significantly increase the likelihood of procuring equipment that delivers reliable, efficient, and cost-effective sludge dewatering for years to come. Due diligence, including site visits to view similar machines in operation and obtaining detailed quotations with clear performance guarantees, is strongly recommended.