The relentless demands of modern manufacturing require equipment that delivers speed, efficiency, and reliability. When it comes to rapidly removing significant quantities of water from textiles, components, or processed materials, a high-speed industrial spin dryer emerges as a critical workhorse in diverse industrial settings.
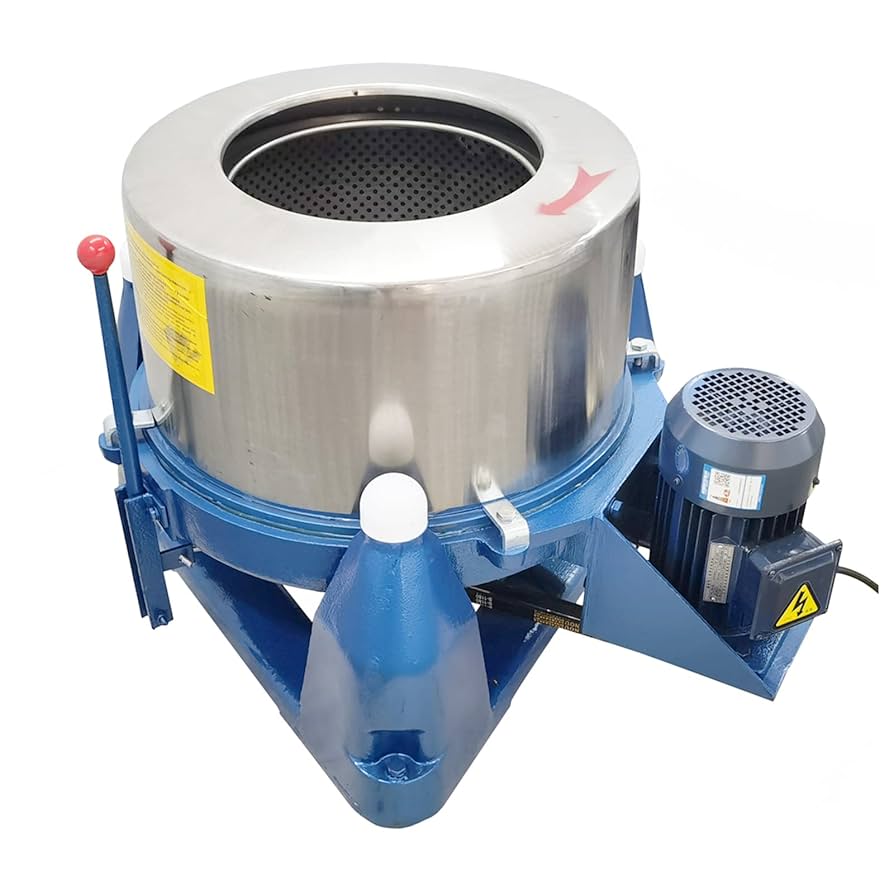
The Power of Centrifugal Force
High-speed industrial spin dryers utilize a fundamental principle: centrifugal force. By rapidly rotating a perforated basket holding the wet items, the machine generates powerful forces that effectively separate water from the load. This force drives the moisture outward, forcing it through the basket’s perforations and into a collection chamber surrounding it.
Speed is the defining characteristic. These units operate at significantly higher revolutions per minute (RPM) than conventional washers or consumer-grade spinners. This intense rotational velocity translates directly into dramatically faster moisture removal cycles. What might take hours in ambient air drying or significantly longer in slower machines can often be reduced to mere minutes, enhancing overall process throughput.
Key Advantages for Industrial Operations
The adoption of high-speed spin dryers offers several tangible benefits for businesses:
- Enhanced Productivity: The drastic reduction in drying cycle times allows for faster turnover of materials. Items processed in minutes are ready for the next stage – packing, finishing, further processing, or shipment – much sooner than traditional methods allow.
- Substantial Energy Savings: Removing the majority of moisture mechanically before any heat-assisted drying phase (like tumble drying) is remarkably energy-efficient. Mechanical water extraction consumes far less power than evaporating the same volume of water using heat. This significantly lowers energy consumption and associated costs, especially for facilities handling large volumes daily.
- Improved End Product Quality: The rapid, forceful action can contribute to a smoother finish in certain textiles and helps prevent the setting of wrinkles or watermarks that slower drying methods might cause. For parts cleaning, quick removal minimizes potential flash rusting or water spotting.
- Reduced Shrinkage & Wear: For textiles, minimizing exposure to prolonged heat significantly reduces the risk of shrinkage and fiber stress, extending the usable life of linens, uniforms, or other textile products.
- Optimized Space Utilization: Due to their fast cycle times, these machines often require less floor space than banks of slower dryers needed to achieve similar throughput.
- Versatility Across Materials: Designed robustly, they handle a wide range of items, from heavy towels and uniforms in commercial laundries to metal parts after washing, plastic pellets, filter media, produce, and other bulk materials requiring quick dewatering.
Design Features for Robust Performance
Industrial spin dryers are engineered for demanding, continuous use. Key features often include:
- Robust Construction: Typically featuring heavy-duty stainless steel or specialized coatings in the basket and casing to withstand high rotational speeds, constant moisture, and aggressive cleaning chemicals.
- High-Capacity Motors & Precision Balancing: Powerful motors drive the basket to the required high speeds. Sophisticated balancing systems ensure smooth operation even with uneven loads, minimizing vibration and wear.
- Advanced Safety Systems: Interlocks prevent the door from opening during operation, and braking systems bring the basket to a safe stop quickly after the cycle ends. Sensors can monitor imbalance and vibration levels.
- Variable Speed Control & Programmable Cycles: Operators can select the optimal speed for different materials and load sizes, ensuring effective extraction without damage. Programmable timers allow for precise cycle control.
- Effective Water Removal Systems: Efficient water collection and drainage systems handle the large volumes of expelled liquid.
Application Areas Beyond Laundry
While heavily utilized in commercial laundries, hotels, and healthcare linen services, high-speed industrial spin dryers find extensive use elsewhere:
- Parts Cleaning & Surface Treatment: Essential for removing rinse water from machined parts, stamped components, and cleaned metal surfaces before coating, painting, or assembly.
- Plastics Processing: Used to dewater plastic pellets, flakes, or powders after washing or crystallization.
- Food Processing: Employed for quick dewatering of washed vegetables, fruits, herbs, or seafood.
- Chemical & Pharmaceutical: Used to quickly remove liquids from filter cakes or bulk solids.
- Recycling & Waste Processing: Effective in dewatering various materials like plastics, rubber, or pulp during recycling operations.
Selecting the Right Machine
Choosing the appropriate high-speed spin dryer requires careful consideration of:
- Load Capacity: The required basket size (volume) to handle typical batch loads.
- Material Type & Fragility: Ensuring the machine’s action is suitable for the items processed (e.g., gentle vs. intensive extraction).
- Required Extraction Level (Residual Moisture Content): Different applications may tolerate more residual moisture than others.
- Throughput Requirements: How many cycles per hour/day are needed to meet production goals.
- Integration: Standalone vs. integration into automated lines.
- Ease of Maintenance & Serviceability: Considering accessibility for cleaning and servicing.
Facility managers and production engineers consistently report that the integration of a modern, high-speed industrial spin dryer significantly streamlines their processes involving wet components, textiles, or bulk materials. The primary advantages observed are the acceleration of workflow due to drastically reduced drying times and the corresponding decrease in energy consumption during subsequent drying phases. This combination of speed and efficiency contributes to lower operational costs and enhanced throughput capacity.
The technology behind high-speed extraction provides industries with a proven, efficient method to tackle the fundamental task of rapid water removal. The ongoing development focuses on further improving energy efficiency, automation features, and user-friendly controls, solidifying their role as indispensable assets in modern industrial processes.